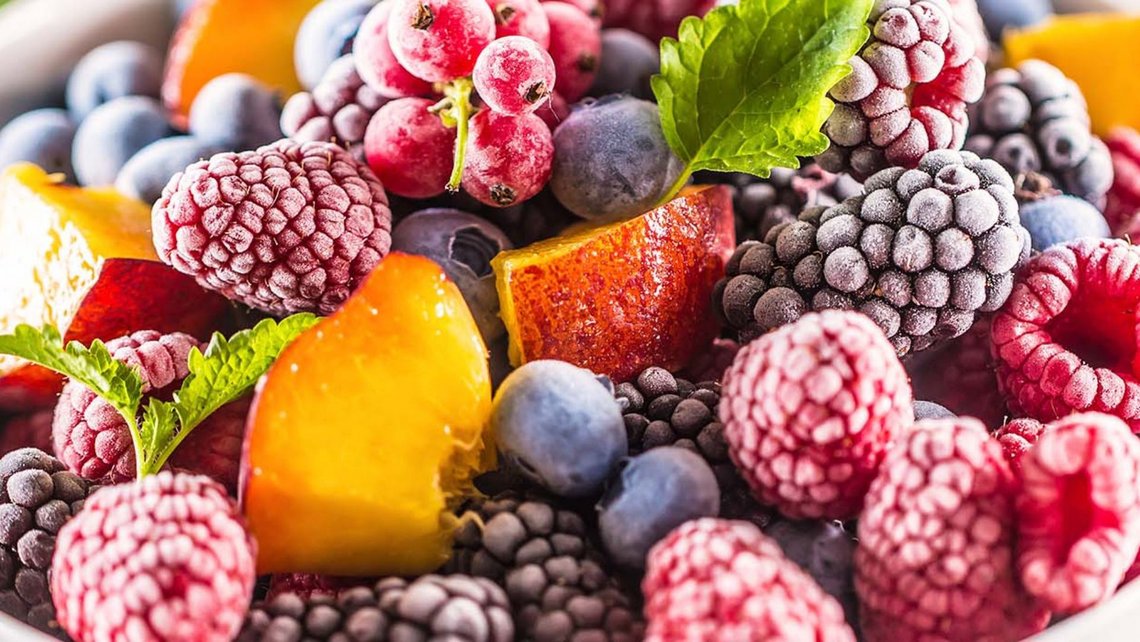
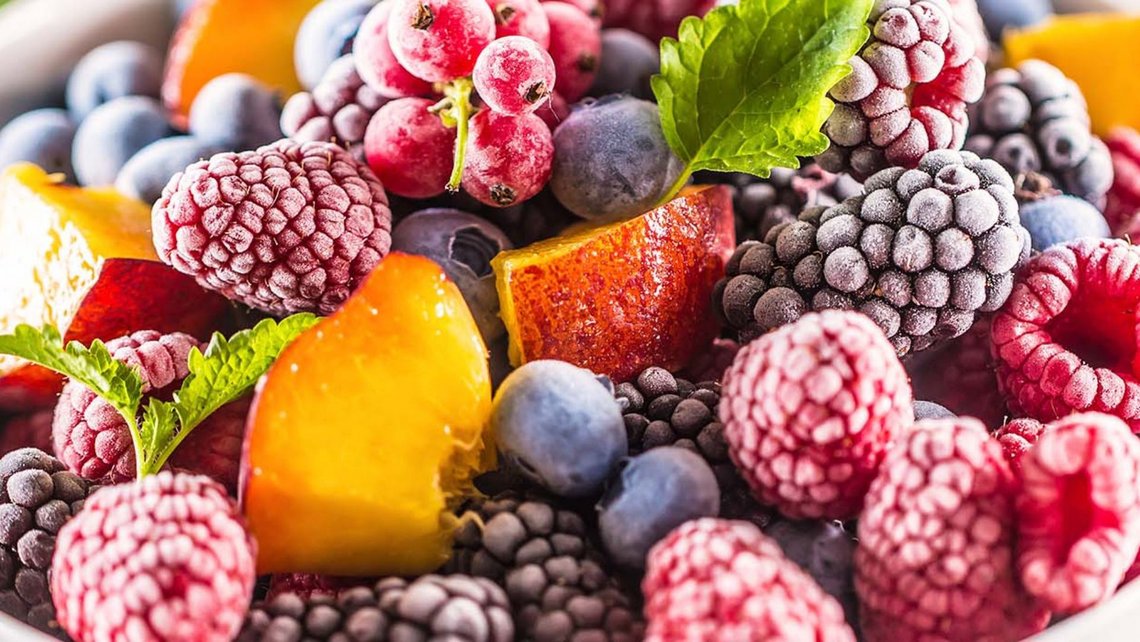
Coop
& TGW Logistics
How Coop and TGW Logistics Improved Energy Efficiency in Cold Chain Logistics
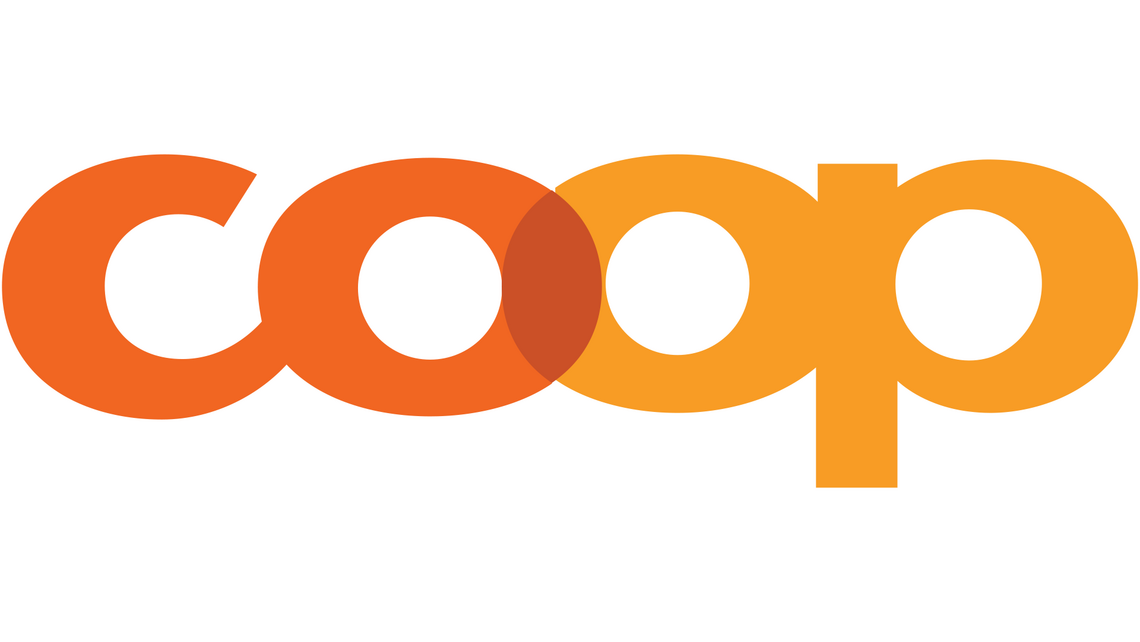
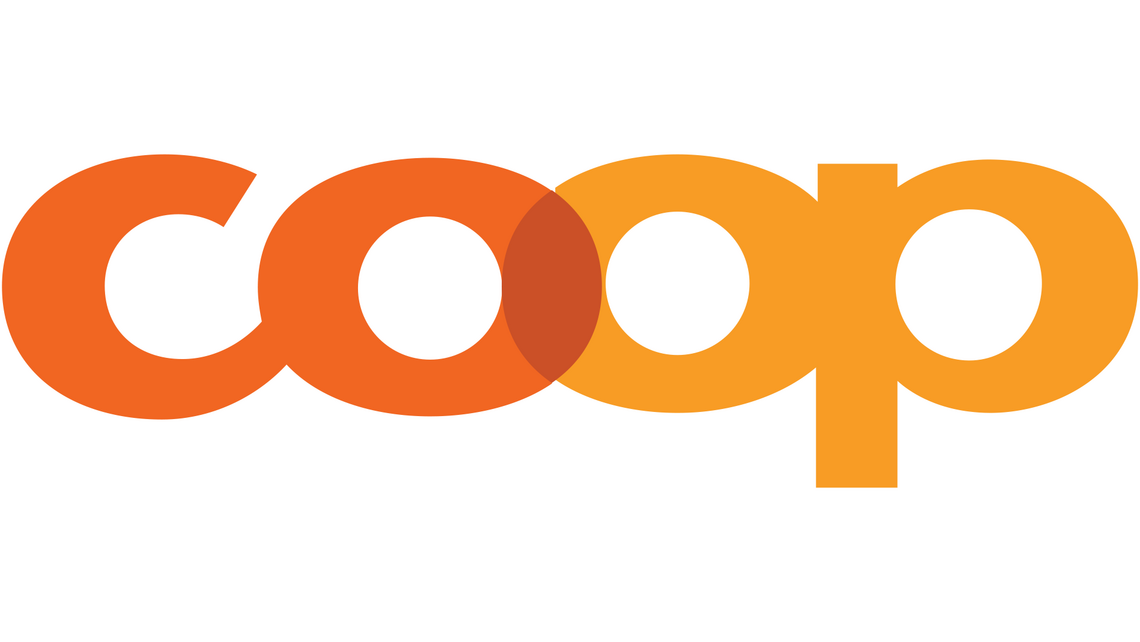
Improved Energy Efficiency
For Coop Genossenschaft, one of Switzerland's largest grocery retailers, operational excellence and sustainability are integral to their business ethos. Their bold mission to centralize their cold chain logistics, optimize energy consumption, and reduce their carbon footprint required an equally bold partner. Enter TGW Logistics.
The result was a state-of-the-art, fully automated distribution center in Schafisheim, near Zurich. This CHF 600 million investment allowed Coop to consolidate regional freezer distribution centers and bakeries, drastically improve efficiency and cut over 10,000 tons of CO₂ annually.
The Challenge: Consolidation in the Name of Optimization
Coop's supply chain is spread across several distribution centers, freezer storage facilities, and bakeries. Managing these separate entities slowed things down, required substantial energy, and made it difficult to achieve sustainability goals. Cold chain logistics management was particularly challenging, with frozen and refrigerated goods requiring precise temperature control, while dry goods and bakery products required different handling.
For Coop, these hurdles went beyond day-to-day grocery logistics. The company set a goal of becoming CO₂ neutral by 2050, which required them to rethink how they managed their entire supply chain. Workplace safety was also a pressing concern, especially for employees working in extremely cold environments. Coop needed an innovative solution to consolidate and transform operations, aligning with their efficiency logistics objectives and operational needs.
The Vision: Turning Complexity into Possibility
From the outset, we recognized the potential to turn Coop’s logistical complexity into a streamlined, energy-efficient, and fully automated solution. More than a consolidation of physical sites, it was a massive overhaul of Coop's operations. We approached the challenge with a vision: to design a grocery logistics center that could handle multiple types of goods in multiple temperature zones with our same standard, proven automation technologies. Coop’s new Schafisheim distribution center would bring together three regional distribution centers, three freezer storage centers, and three bakeries - all under one roof. But centralization was just the beginning.
The Solution: A Unified, Automated Logistics Hub
At the heart of Coop’s new operations was a fully automated logistics system designed and implemented by TGW Logistics. The distribution center, which spreads across two connected buildings, acts as the nerve center for all of Coop’s supply chain operations. Our automated systems handle everything and minimize human intervention while maximizing productivity.
- Frozen Goods Automation: The system was developed to handle frozen goods as cold as -23°C. It is fully automated for consistent temperature control and minimal manual involvement in a hazardous environment.
- Refrigerated Goods Fulfillment: Refrigerated goods are managed in a 2°C environment, where TGW Logistics’ automated fulfillment systems maintain food quality while reducing energy consumption.
- Dry Goods and Manual Picking: Dry goods are stored and handled via a pallet warehouse with manual picking, integrated seamlessly into the overall material flow.
- Bakery and Confectionery Production: The bakery facility alone produces 50,000 tons of baked goods annually, all while operating within a highly automated environment.
- Empty Packaging Center: A dedicated system processes and sorts empty containers, maintaining sustainability at every stage of the supply chain.
Perhaps the most innovative feature is the 160-meter bridge connecting the two main building complexes. The bridge ensures that the flow of goods between sections remains fluid and uninterrupted, keeping operations running smoothly and efficiently.
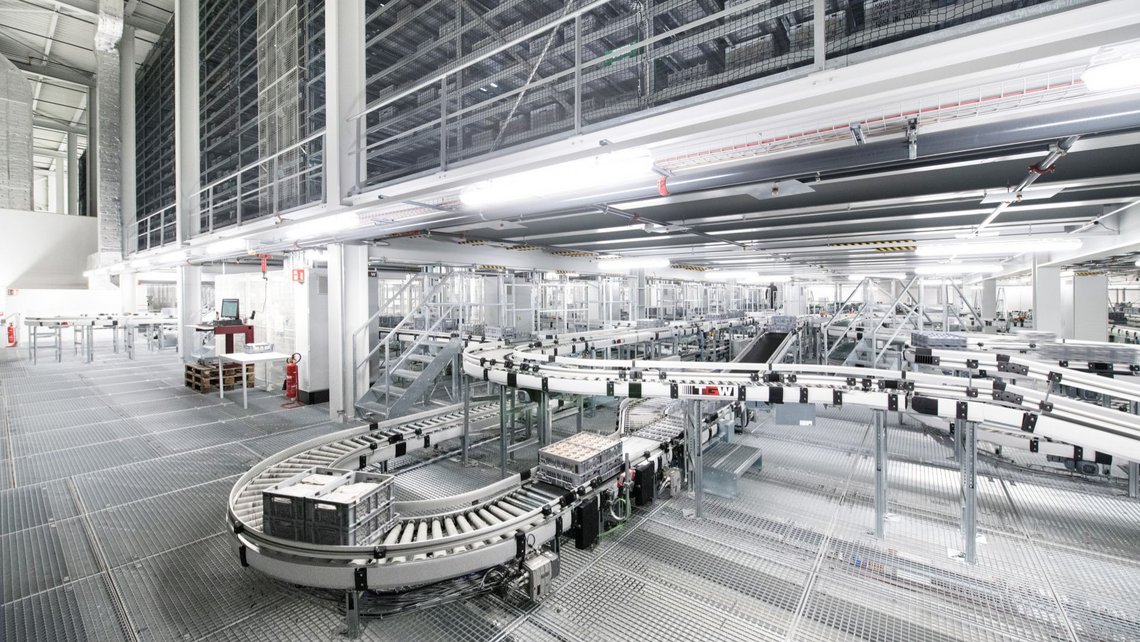
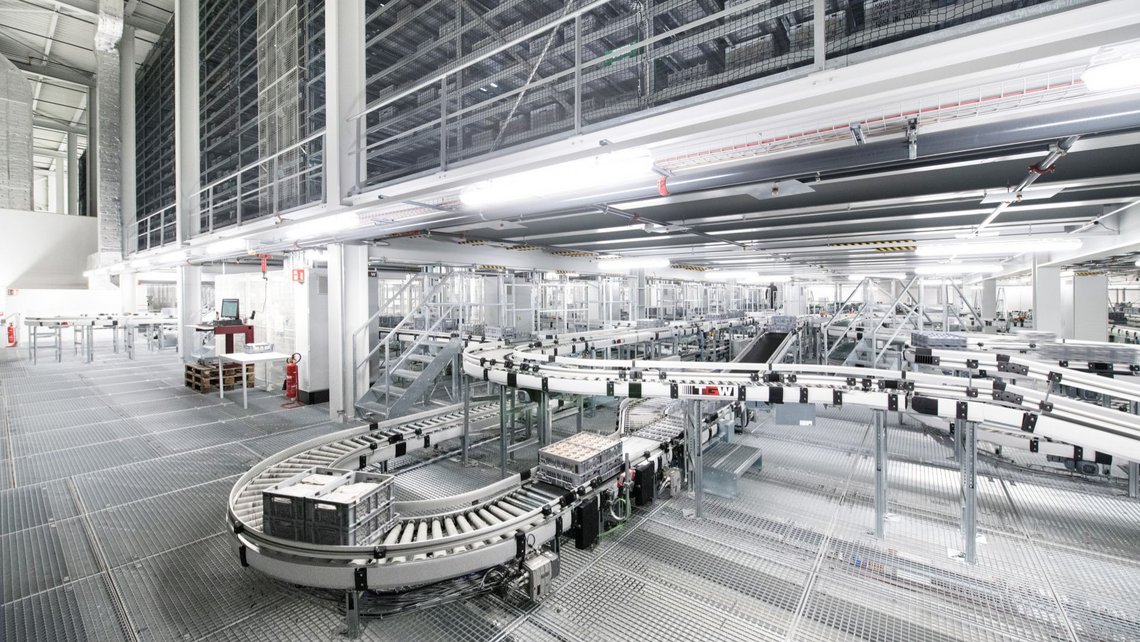
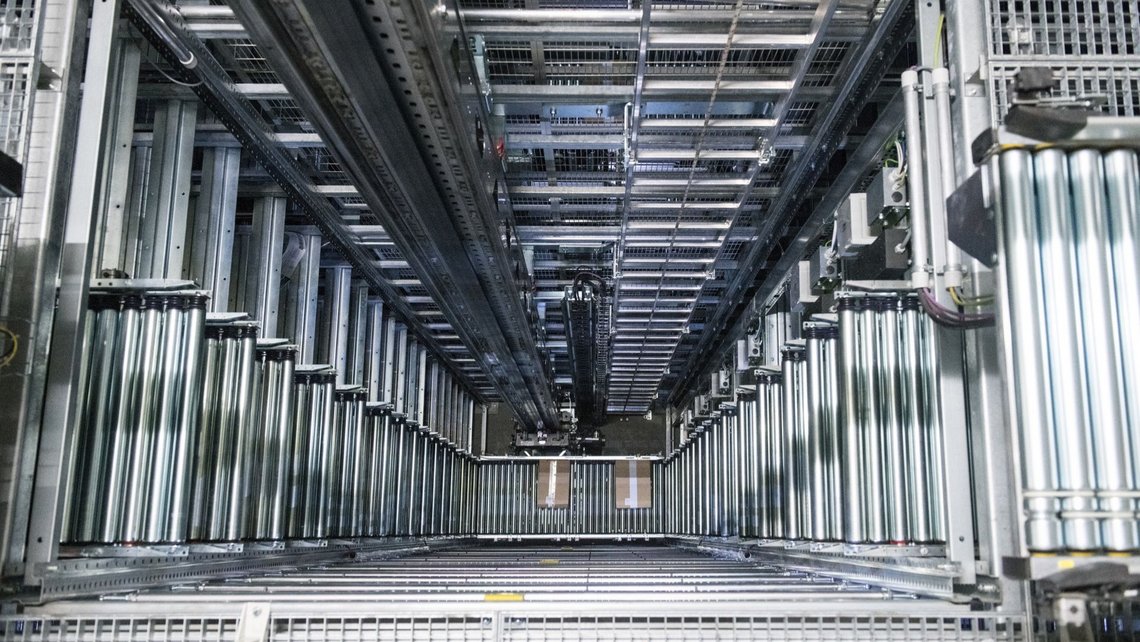
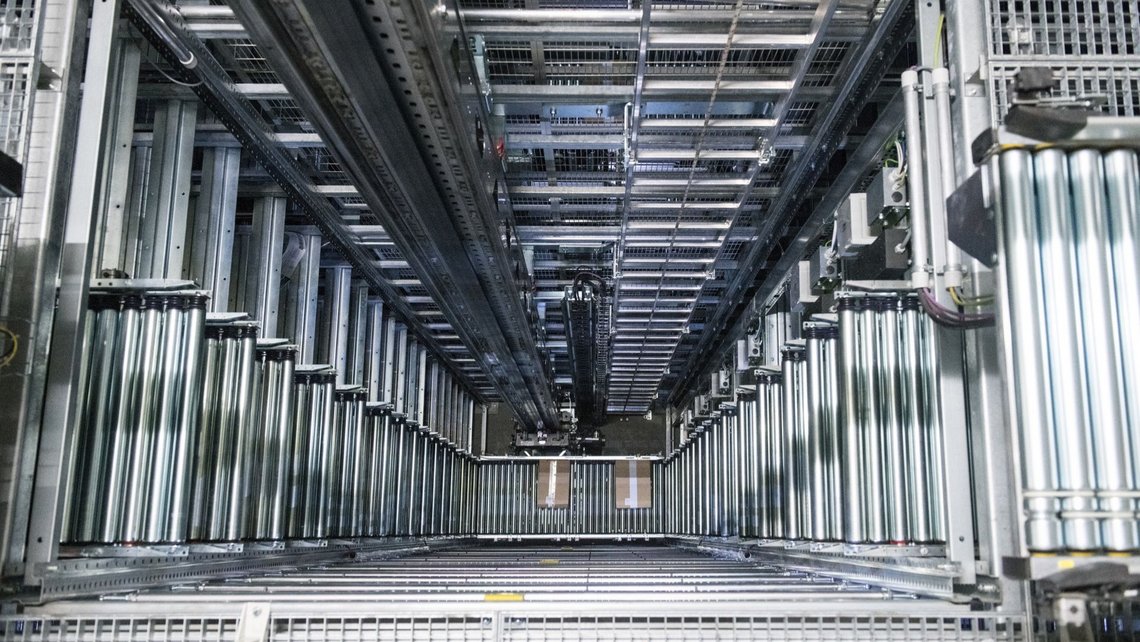
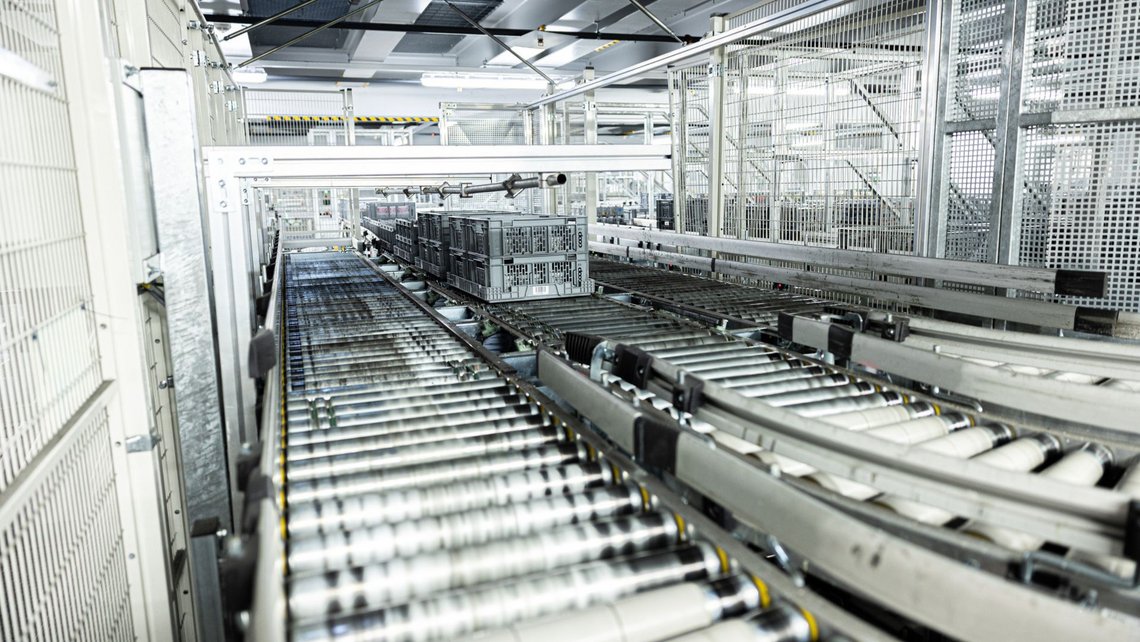
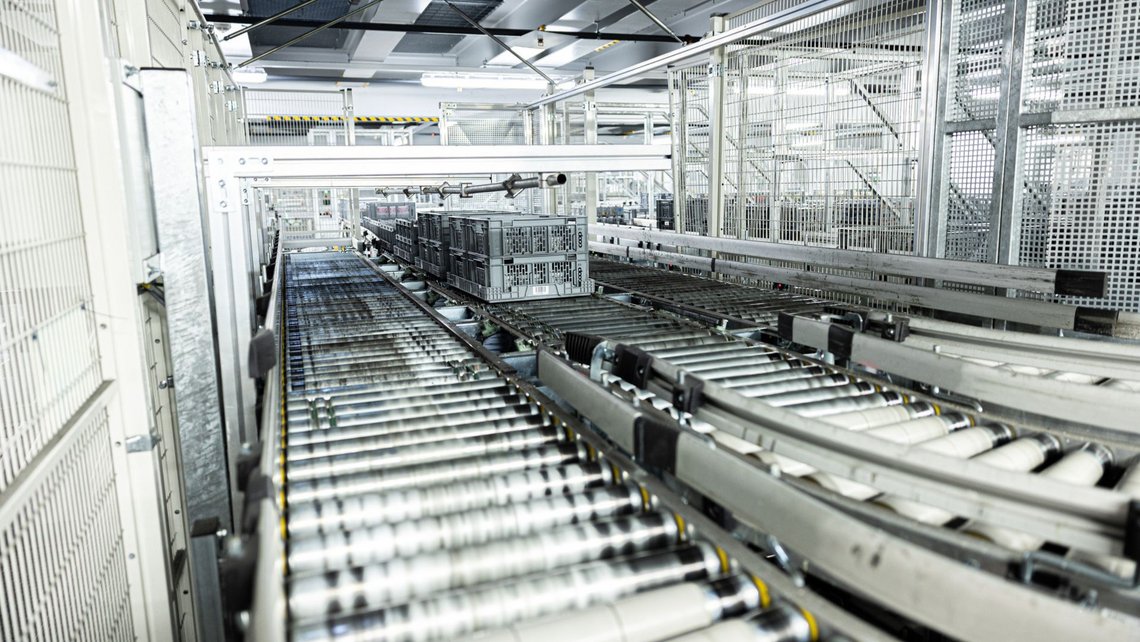
Integrating Innovation into Grocery Logistics
While the automation of logistics processes was a game-changer for Coop, the warehouse solutions also supported their sustainability goals. By consolidating operations and implementing TGW Logistics’ smart automation, Coop achieved:
CO₂ Reduction
The new center reduced Coop’s carbon footprint by over 10,000 tons annually—an essential step toward achieving the company’s 2050 goal of CO₂ neutrality.
Energy Efficiency in Cold Storage
TGW Logistics implemented an innovative, energy-saving approach in the freezer shuttle warehouse. By reducing the oxygen content to 14% and optimizing the temperature zones to be “as cold as necessary, but no colder,” the facility minimized the energy required to maintain precise temperature control.
Workplace Safety and Ergonomics
The high degree of automation significantly improved working conditions for employees, especially in temperature-controlled areas. With fewer workers required in these environments, Coop drastically reduced the risks and costs associated with extreme temperatures.
The Results: High-Performance and Energy Efficiency Achieved
Coop’s fully automated logistics center is now a benchmark for how automation and sustainability can go hand-in-hand in the world of grocery logistics. Thanks to TGW Logistics’ automation and energy-saving designs, Coop has significantly reduced its total cost of ownership, leveraging optimized energy usage for a better return on investment. As Coop looks ahead, they do so with confidence in our partnership. Our comprehensive Lifetime Services package will continue to support Coop's operations for years to come, providing complete maintenance coverage so the automated warehouse solutions remain at peak performance.
Contact us today
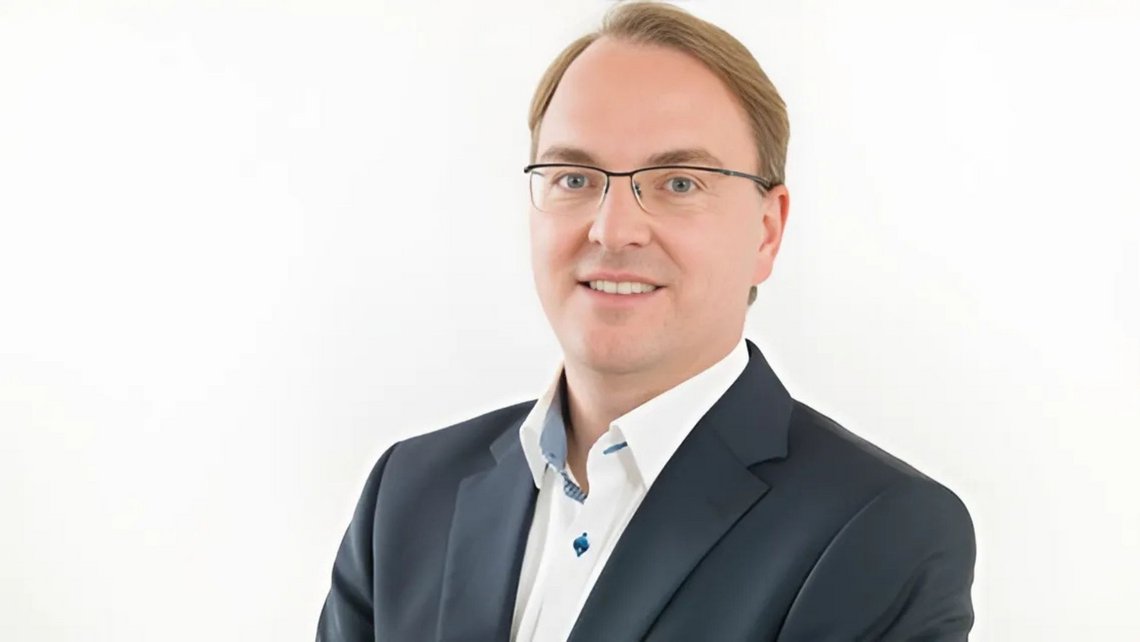
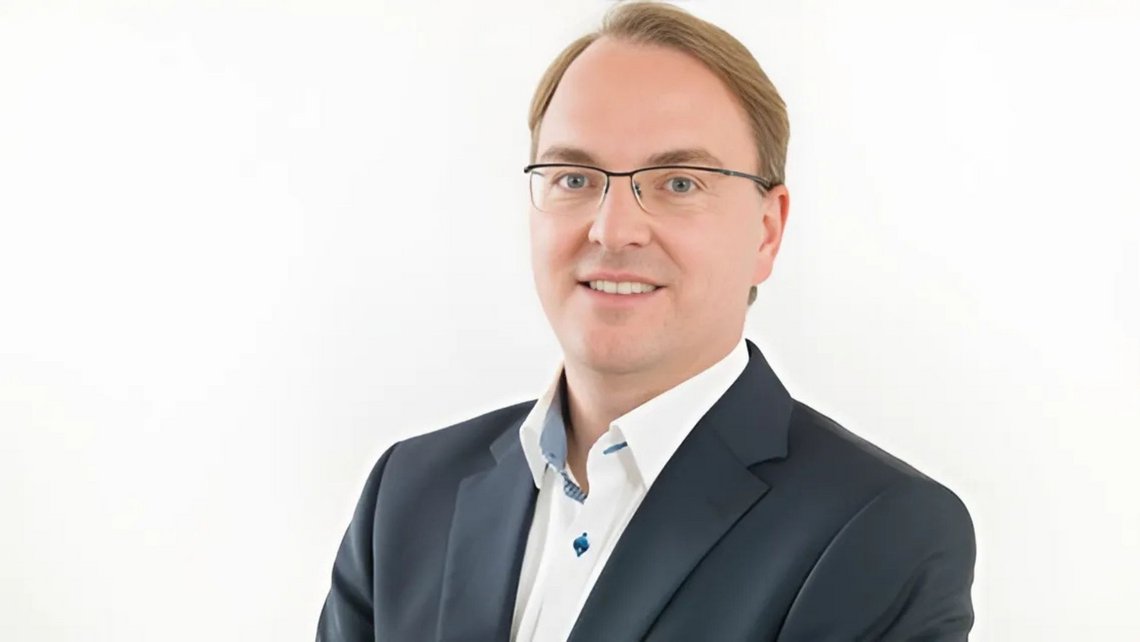
Michael Schedlbauer
Vice President Business Development Grocery
TGW Logistics is a foundation-owned company headquartered in Austria and a global leader in warehouse automation and warehouse logistics. As a trusted systems integrator with more than 50 years of experience, we deliver end-to-end services: designing, implementing, and maintaining fulfillment centers powered by mechatronics, robotics, and advanced software solutions. With over 4,500 employees spanning Europe, Asia, and North America, we combine expertise, innovation, and a customer-centric dedication to help keep your business growing. With TGW Logistics, it's possible to transform your warehouse logistics into a competitive advantage.