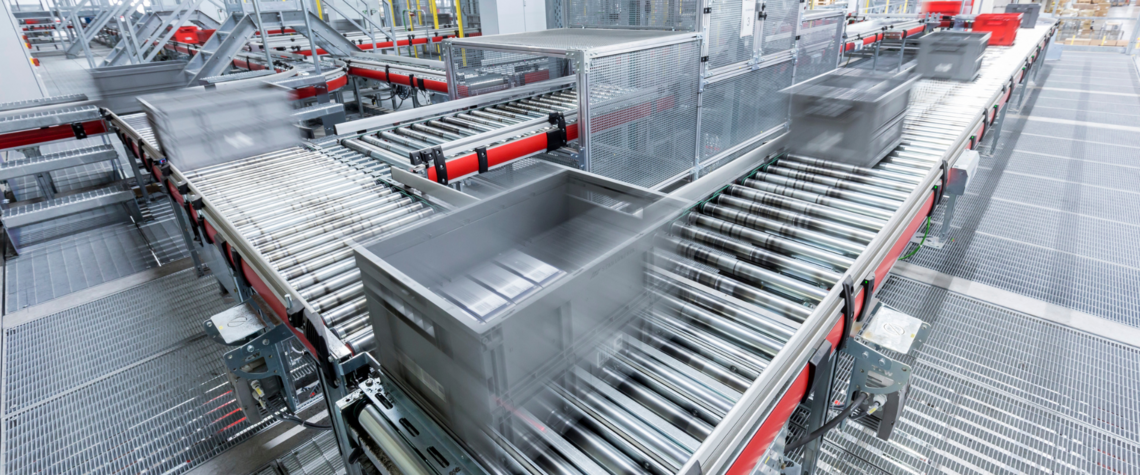
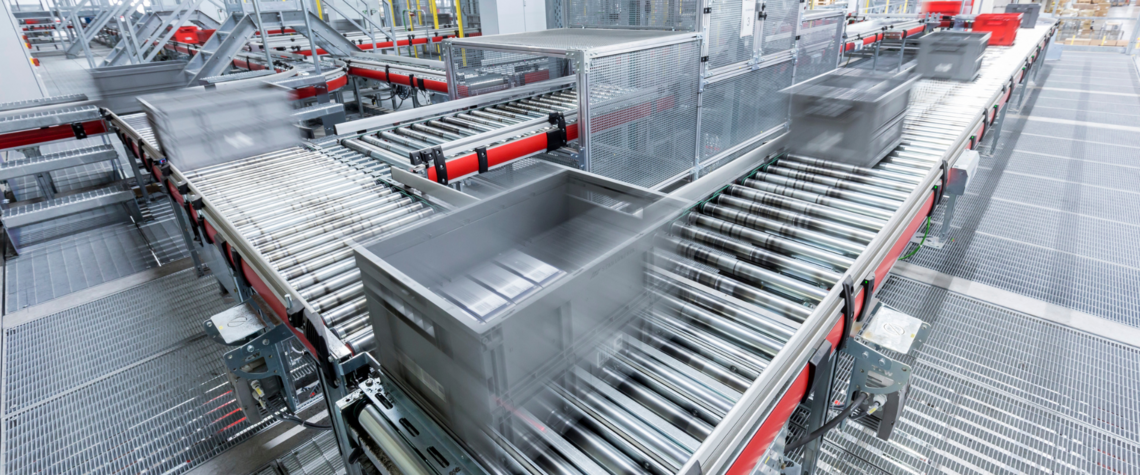
The warehouse and logistics industry faces an unprecedented labor shortage that disrupts supply chains, material handling operations and increases operational costs. This challenge is primarily driven by significant demographic shifts, with the U.S. Bureau of Labor reporting that 23% of the U.S. population will be 65 or older by 2030.
The numbers tell a concerning story: labor participation rates will drop over 1% from 2020 to 2030, eliminating more than 5 million potential workers from the labor pool.
As unemployment rates remain below 5% since the fall of 2021, businesses must develop innovative strategies to attract and retain warehouse workers while reducing dependence on an increasingly unpredictable labor market.
Key Trends Impacting The Warehouse Labor Market
Already, the median age in the U.S. is 39. This demographic shift is fundamentally altering the warehouse labor market. Baby Boomers are retiring at record rates, creating a significant voice in the workforce that younger generations simply aren’t filling in the same roles.
Manual labor in warehouses, especially in temperature-controlled environments where conditions can be physically challenging, historically appeals to younger workers. The role of an order picker is especially demanding, requiring constant movement throughout shifts. With 25% of the U.S. population approaching retirement age, the available pool of candidates physically suited for traditional warehouse roles continues to contract.
The implications are clear: businesses operating labor-intensive warehouse models face a steadily diminishing talent pool, forcing a fundamental reconsideration of how work gets done.
Tellingly, since 2022, data from the U.S. Chamber of Commerce shows job openings exceeding unemployed workers by approximately 2 million positions. This gap creates an environment where workers can be increasingly selective, challenging employers' recruitment and retention efforts. When job seekers have choices, physically demanding order picker positions with traditional shift structures become more challenging to fill and maintain.
Historical data indicates this imbalance between available workers and open positions will persist outside of major economic downturns, making it a long-term structural challenge rather than a temporary disruption.
The U.S. Bureau of Labor Statistics projects that 3.3 million additional jobs will emerge in healthcare and social services alone by 2030, with millions more in tech, hospitality, and renewable energy. These growing industries actively compete for the same limited labor pool that warehouses traditionally rely upon.
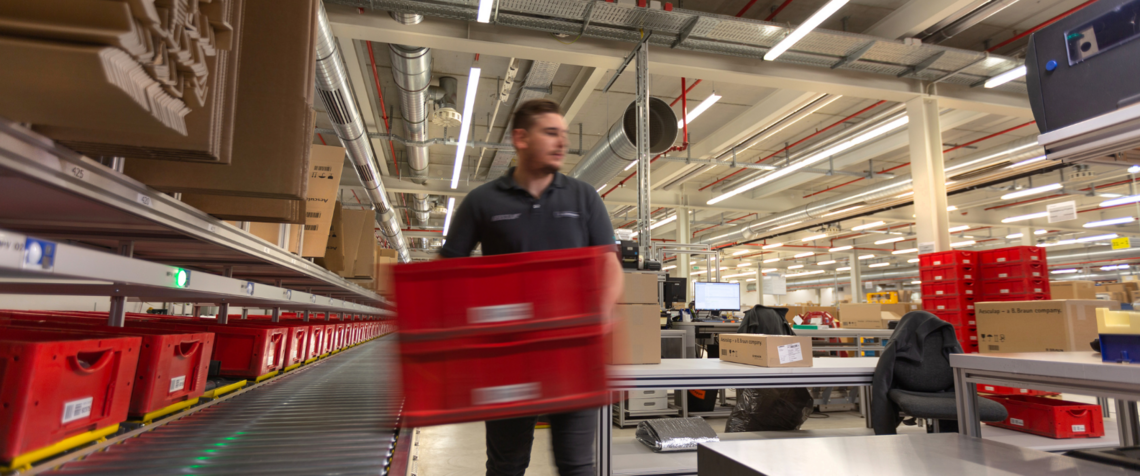
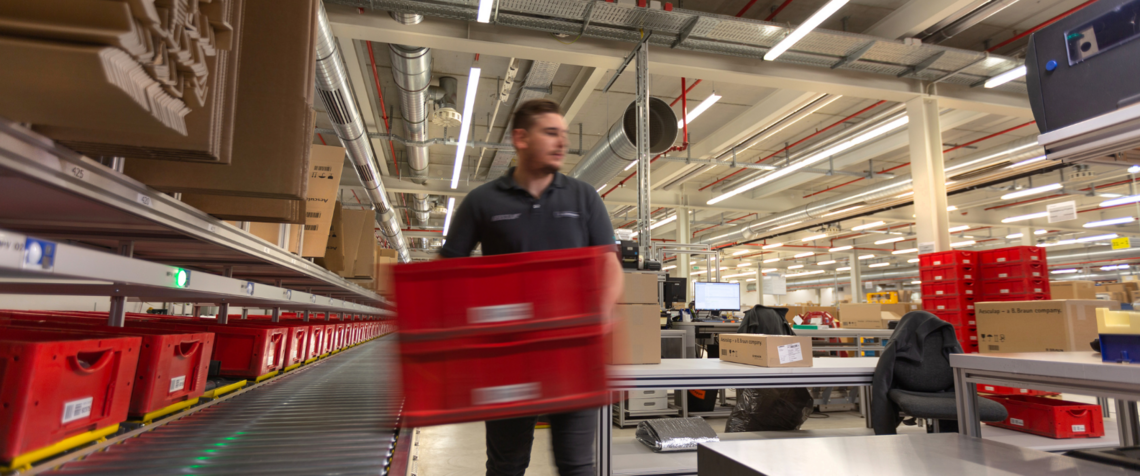
Challenges In Hiring And Retaining Order Pickers
According to Pew research data, job resignation rates spiked to historic highs in 2021 and 2022 across all age groups, with the most dramatic increases among employees under 35 years old, precisely the demographic traditionally filling warehouse positions. This resignation wave has created interconnected challenges for warehouse operators.
Competition for warehouse talent has intensified dramatically. Traditional warehouse employers now compete directly with industries offering more attractive work environments and competitive compensation packages. When facing multiple job options, potential employees increasingly choose positions in retail, healthcare, or service industries over conventional warehouse roles like being an order picker.
Worker priorities have evolved significantly. Today’s employees increasingly prioritize:
- Less physically demanding environments
- Flexible scheduling options
- Clear career advancement pathways
- Competitive compensation packages
- Better work-life balance
Traditional warehouse options frequently struggle to compete on these priorities, placing them at a distinct disadvantage in the battle for talent.
Companies have implemented higher wages, sign-on bonuses, retention incentives, and expanded benefits to remain competitive in recruitment. These cost increases directly impact profit margins, and the expense of turnover further compounds these costs.
The physical demands of traditional warehouse work create another significant barrier. Manual lifting, walking long distances over a shift, repetitive motions, and challenging environments contribute to worker fatigue, injury risk, and, ultimately, dissatisfaction. Following OSHA safety guidelines and implementing proper ergonomic practices can help mitigate these risks while improving workplace conditions for order pickers.
An industry rule of thumb indicates that in conventional manual warehouse operations, pickers typically spend 60% of their time walking and only 40% picking—an inefficient model that creates unnecessary physical strain.
Together, these challenges create a self-perpetuating cycle: physically demanding work leads to fatigue and turnover, which increases costs and recruitment challenges. Breaking this cycle requires rethinking warehouse operations rather than simply adjusting compensation packages.


Solutions For Hiring And Retention
Many warehouse operators initially respond to labor challenges by increasing compensation. Offering higher wages, signing bonuses, and expanded benefits packages can attract workers in the short term. Still, this approach faces diminishing returns as competitors match or exceed these offers, creating unsustainable cost structures across the industry.
A more sustainable approach combines targeted compensation strategies with broader retention initiatives. Programs such as retention bonuses tied to tenure milestones, flexible scheduling options that accommodate diverse lifestyles, and defined career development pathways that show advancement potential can significantly improve retention metrics without relying solely on base wage increases.
However, the most effective long-term solution involves fundamentally automating the warehouse work environment. Modern warehouse automation systems create five distinct advantages in addressing labor challenges:
- Automation expands the labor pool by reducing physical demands through ergonomic workstations and handling systems, opening opportunities for workers with physical limitations.
- Productivity soars when automation eliminates walking time (60% of traditional picking activity), enabling one worker to accomplish what previously required 2.5 workers.
- Technology-focused roles create more appealing environments with higher satisfaction and lower injury rates, directly improving retention and reducing burnout.
- Training time drops dramatically—from weeks to as little as 20 minutes—with intuitive systems like pick-to-light and goods-to-person, enabling faster onboarding and flexibility.
- Workers freed from routine tasks can be cross-trained for higher-value positions, creating better career development paths.
The TGW Approach: Investing in People Through Automation
People remain the core of every warehouse operation. The most effective automation strategies complement human workers rather than simply replacing them, creating an environment where technology and people work together to achieve optimal outcomes.
TGW Logistics approaches warehouse automation with this human-centered philosophy. Their solutions are designed to make warehouse jobs easier and more attractive while improving operational efficiency. This approach reflects a deep understanding that addressing labor challenges requires more than technological innovation—it requires technology that enhances human potential.
The benefits of this people-centered automation approach are multifaceted:
- Warehouse positions become accessible to a broader workforce when physical requirements are reduced through ergonomic workstations and automated material handling systems.
- Productivity per worker increases dramatically as automation eliminates non-value-added activities like excessive walking, allowing businesses to operate efficiently with fewer total staff positions.
- Employee satisfaction improves when physically demanding tasks are automated, creating more engaging work environments and directly reducing turnover rates.
- Operational costs decrease through optimized workflows, reduced training requirements, and lower recruitment expenses.
For many TGW customers, the savings realized through reduced labor costs, minimized training expenses, and lower turnover rates constitute most of their automation ROI. These organizations have discovered that investments in automation technology provide more consistent and predictable returns than continually increasing compensation packages to solve labor challenges.
As labor markets evolve, the most successful warehouse operations will leverage automation not just as a productivity tool but as a strategic solution to hiring and retention challenges. By investing in technologies that enhance rather than replace human capabilities, businesses can navigate labor shortages while creating more sustainable and attractive work environments.
Ready to transform your warehouse operations?
Discover how automation can solve your labor challenges while boosting productivity and employee satisfaction. Contact TGW Logistics now to start building your future-ready warehouse.
TGW Logistics is a foundation-owned company headquartered in Austria and a global leader in warehouse automation and warehouse logistics. As a trusted systems integrator with more than 50 years of experience, we deliver end-to-end services: designing, implementing, and maintaining fulfillment centers powered by mechatronics, robotics, and advanced software solutions. With over 4,500 employees spanning Europe, Asia, and North America, we combine expertise, innovation, and a customer-centric dedication to help keep your business growing. With TGW Logistics, it's possible to transform your warehouse logistics into a competitive advantage.