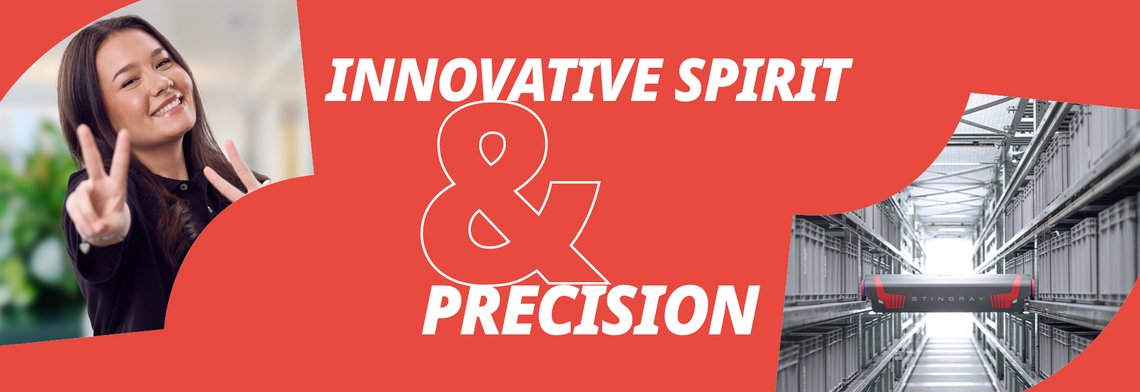
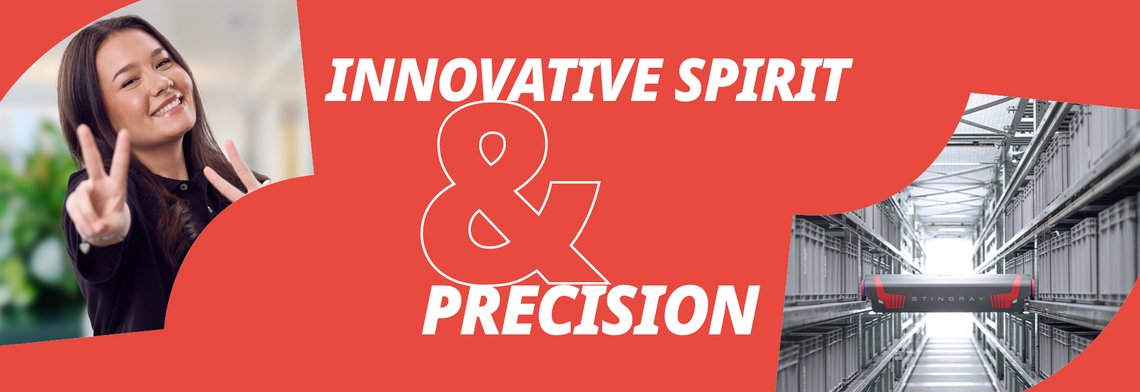
Warehouse Solutions That Grow With You
Overcome any intralogistics challenge with the seamless integration of intelligent software, high-quality products, proven systems, and innovative services offered in our comprehensive portfolio. As your business grows, our warehouse solutions adapt to your supply chain management needs - turning your warehouse into a powerhouse.
- Customers benefit from our proven products and services that streamline their fulfillment process. Intelligent software guides this process for the most efficient material handling solutions, from inbound to storage to order picking to outbound.
The services team ensures automated warehouse systems are updated and run efficiently today, tomorrow, and well into the future. Our expert service teams in the areas On-Site services, Field Services, Remote Services, Spare Parts Services, Training Services and Retrofit & Extension Services are dedicated to enable you to meet your business goals, every step along the way.
Our warehouse management software WERX ensures the optimum flow of goods and low cost per pick. We consider every stage of every product’s lifecycle - from design to manufacturing to implementation to Lifetime Services - with a constant focus on total cost of ownership. Experience the ROI advantages of automated warehouse systems, especially with our unmatched 10-year warranty period.
Our portfolio showcases customizable ways to revolutionize your warehouse. From inbound to outbound, our innovative products and services can transform your warehouse into a powerful, efficient hub of seamless fulfillment - endless possibilities for maximum performance.
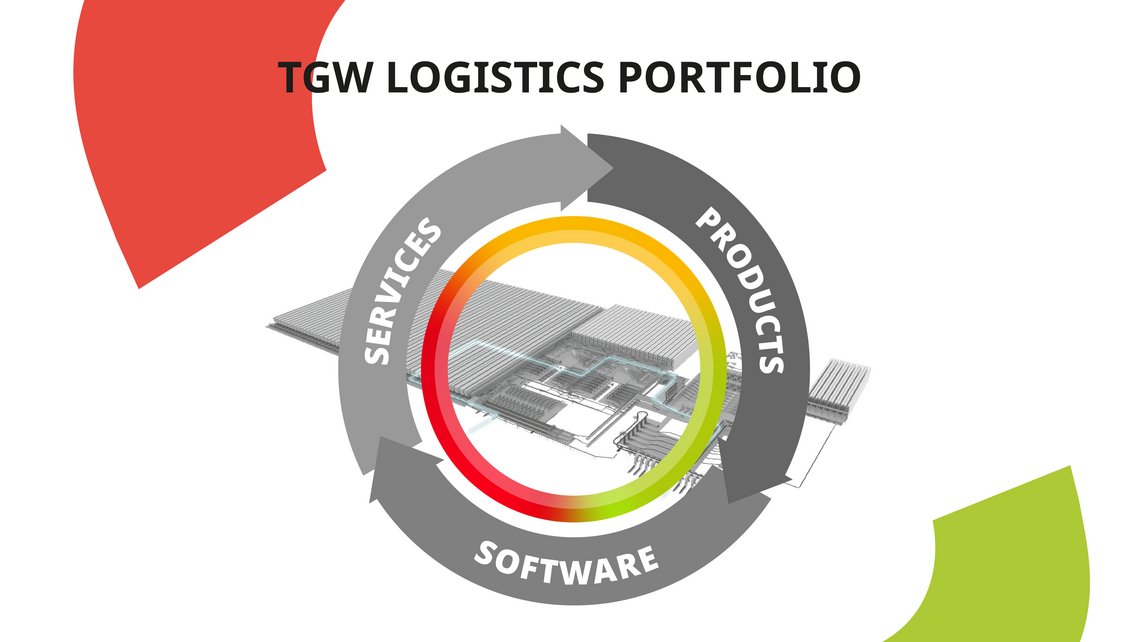
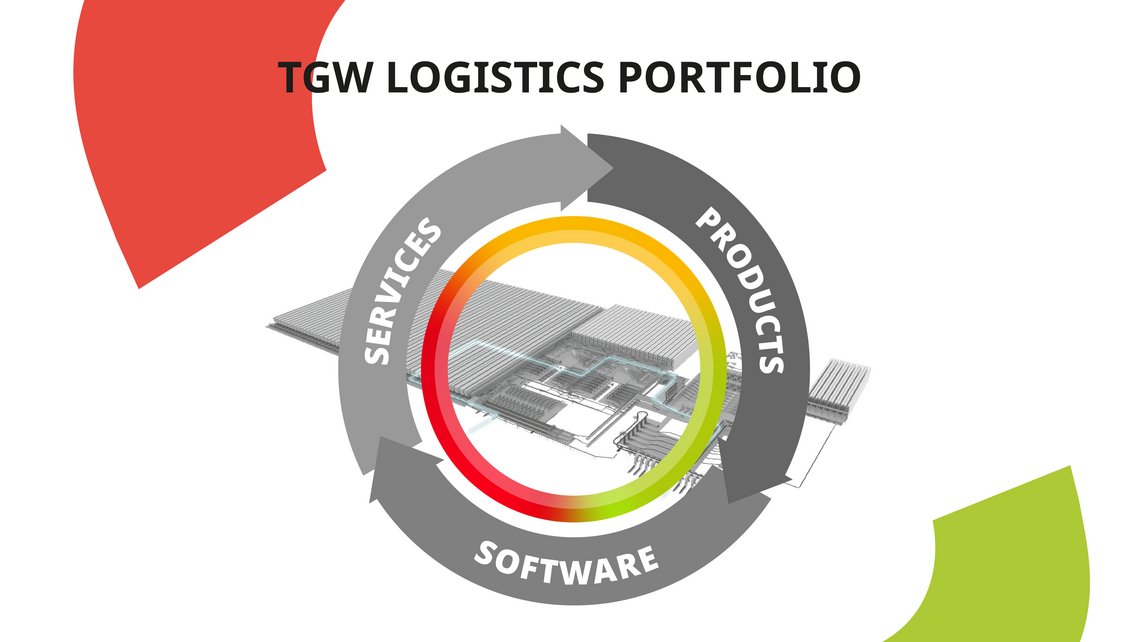
Discover how our unique combination of products, software and services equips you with everything you need to make the impossible possible.
Delivering a Portfolio of Proven Warehouse Solutions
TGW Logistics is your trusted partner for tailored and highly automated warehouse systems. Our comprehensive portfolio showcases various products, software, and services to revolutionize warehouse logistics. Whether you're seeking to streamline end-to-end operations or need specific subsystems to enhance your capabilities, we have a solution for every challenge.
TGW Logistics is a foundation-owned company headquartered in Austria and a global leader in warehouse automation and warehouse logistics. As a trusted systems integrator with more than 50 years of experience, we deliver end-to-end services: designing, implementing, and maintaining fulfillment centers powered by mechatronics, robotics, and advanced software solutions. With over 4,500 employees spanning Europe, Asia, and North America, we combine expertise, innovation, and a customer-centric dedication to help keep your business growing. With TGW Logistics, it's possible to transform your warehouse logistics into a competitive advantage.