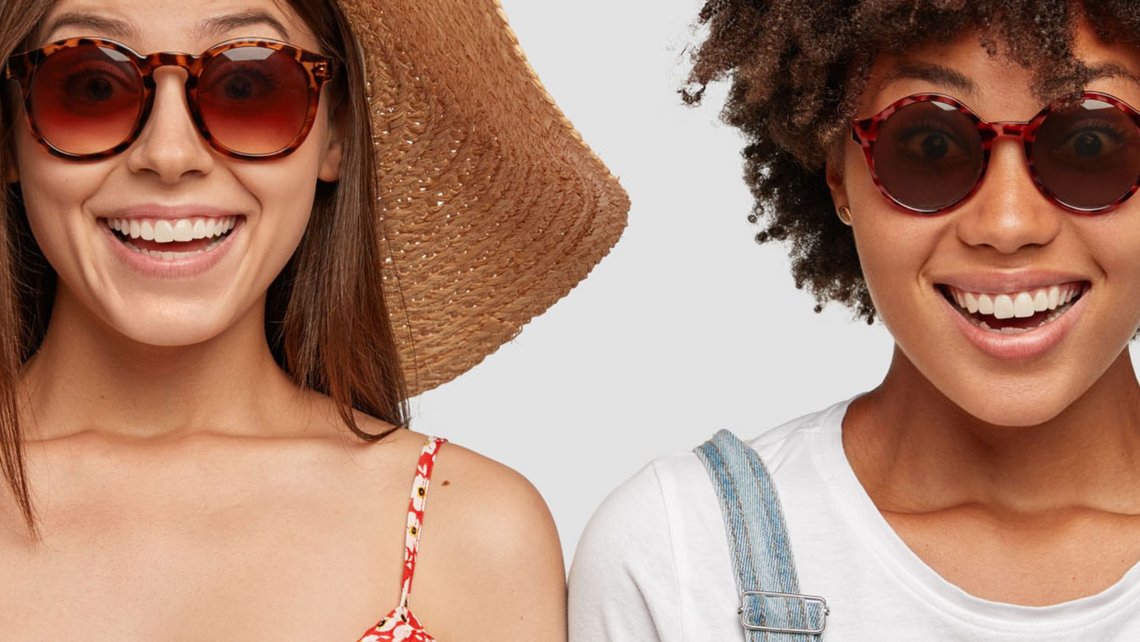
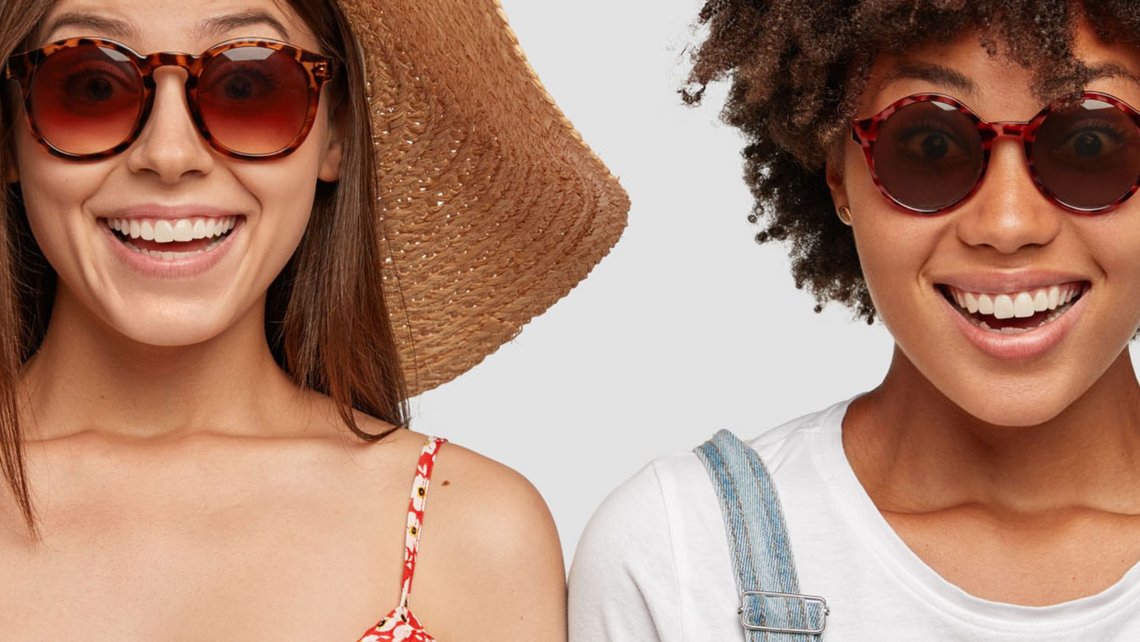
Gap Inc.
& TGW Logistics
Gap Inc. Hits New Performance Levels with TGW Logistics


Automated Material Handling
Gap Inc. has grown from a single retail store in 1969 to one of the largest fashion retailers in the world and includes the brands Gap, Banana Republic, Old Navy, and Athleta. When Gap wanted to reduce the number of manual touches across their distribution centers for more efficient operations, they partnered with TGW Logistics. Over the past eight years, Gap has invested in automated material handling in their U.S. fulfillment centers in Fishkill, Fresno, Gallatin, and Groveport, as well as their Canadian fulfillment center in Brampton.
A Milestone in Material Handling
Gap’s retail and ecommerce orders in North America are handled through decentralized distribution centers. They decided to automate when they noticed their manual processes leading to slowdowns and inefficiencies.
To optimize inbound logistics and storage processes, Gap invested in automated solutions that reduced the number of touches by seven compared to manual systems. With automated goods receiving, operators only need to unload trailers before products are ready to be picked for customer orders.
Gap set a milestone for operational performance, leading them to upgrade seven North American distribution centers.
Benefits of Automation
One-Touch Receiving
Gap eliminated manual touches before picking with One-Touch Receiving, reducing costs while improving the speed and quality of their fashion logistics.
Automated Material Handling
Finding enough operators for their fulfillment centers was a challenge. Using our automated solutions for material handling, inbound logistics now relies less on labor, leading to uninterrupted operations even during peak times.
How TGW Logistics Made it Possible
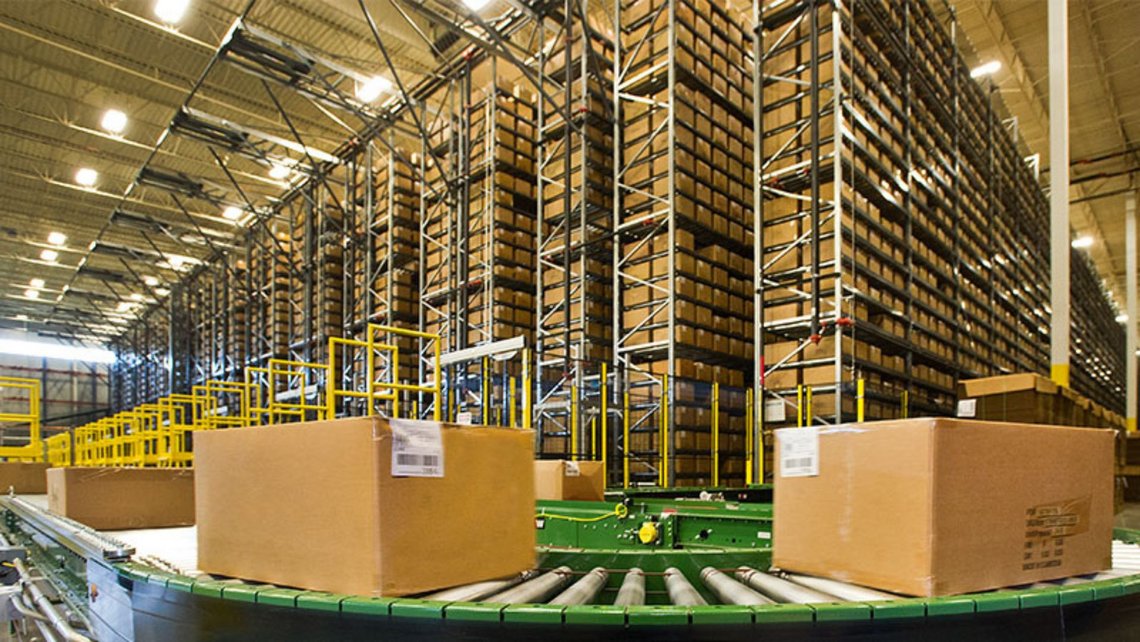
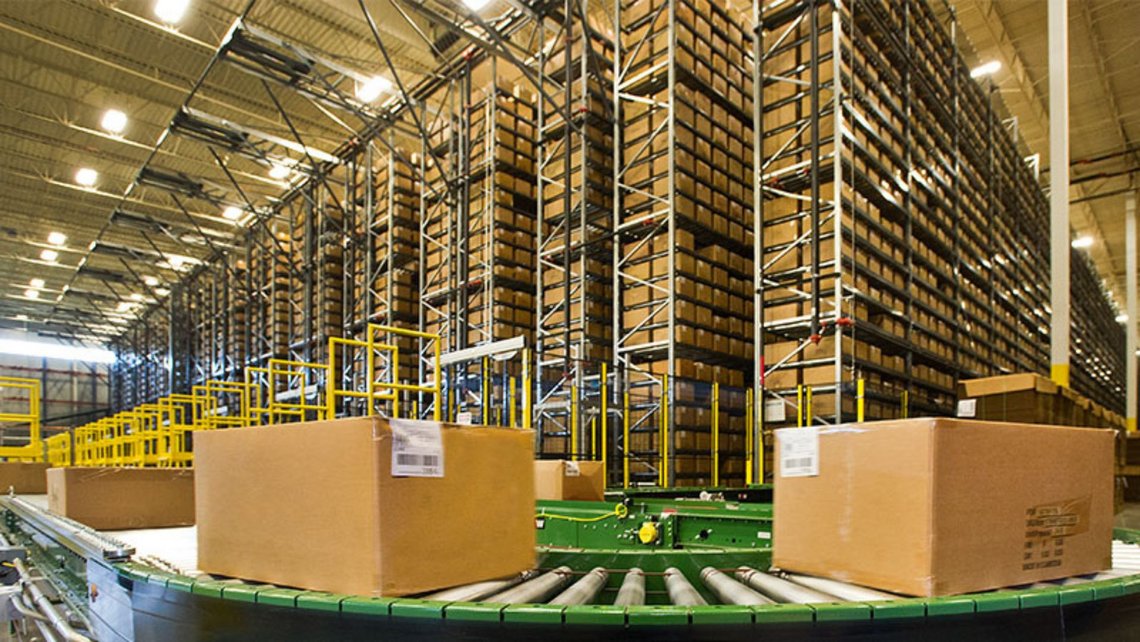
Fast & Efficient Operations with One-Touch Receiving
By implementing One-Touch Receiving, our standardized inbound storage system for material handling and goods receiving processes, Gap saw a return on their investment in less than two years and eliminated seven of eight manual touches. Cartons are unloaded from the truck and placed directly on an extendable conveyor belt before quality inspection and scanning. Once in the system, a conformity check compares delivery quantity with order quantity. Cartons are stored and retrieved with a mini-load system consisting of 36-ft. tall, high-performance cranes, which ensure a cost-effective single carton handling, avoiding labor-intensive operations.
Improved Sorter Replenishment Process
The mini-load system supplies a unit sorter, which sorts the SKU ordered by the stores into shipping cartons. Any source cartons that still contain products are returned into a temporary storage buffer based on shuttles that are effectively capable of handling the opened cartons.
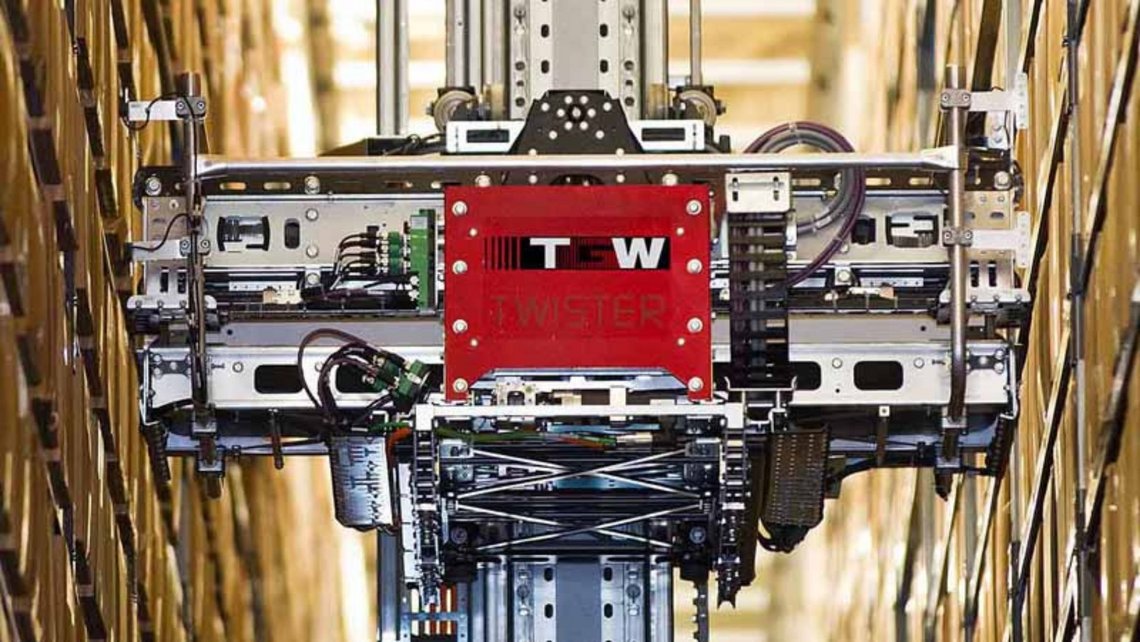
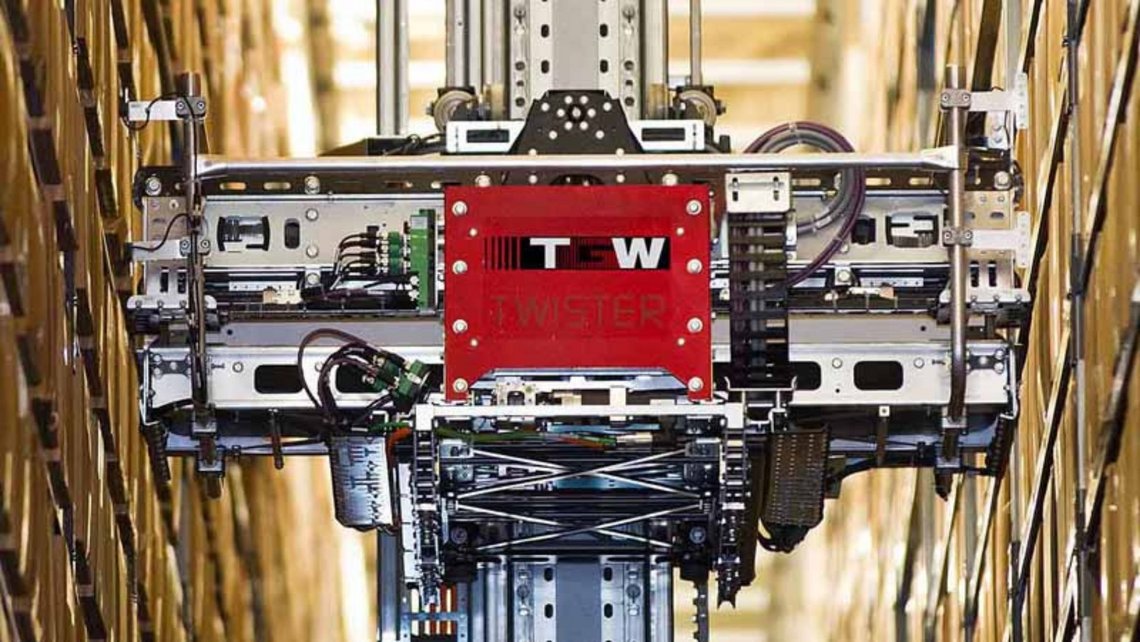
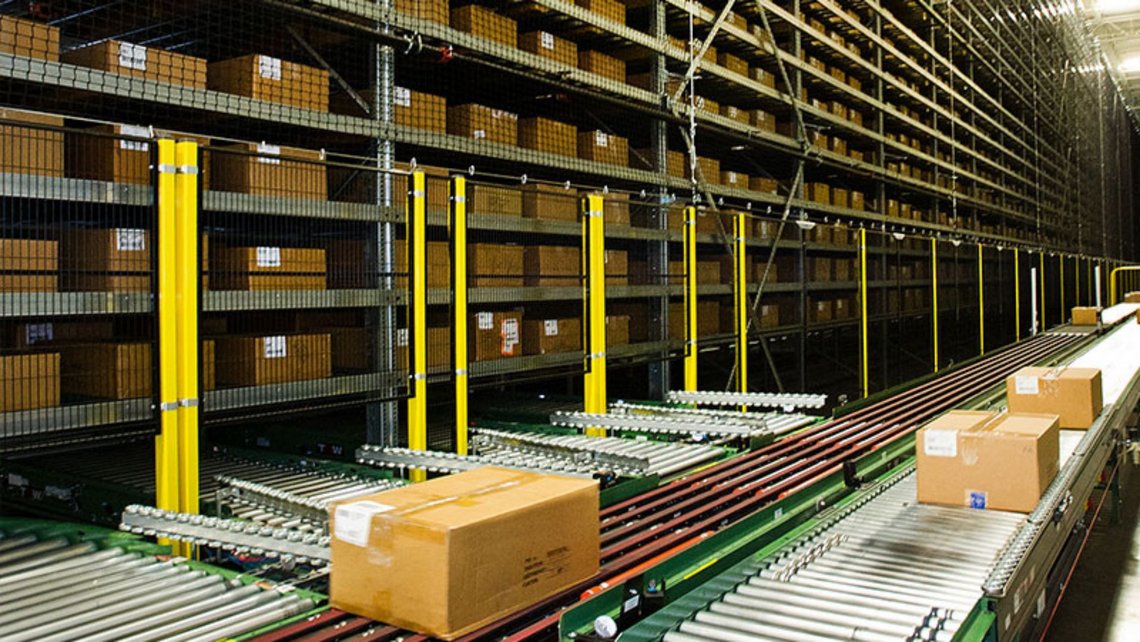
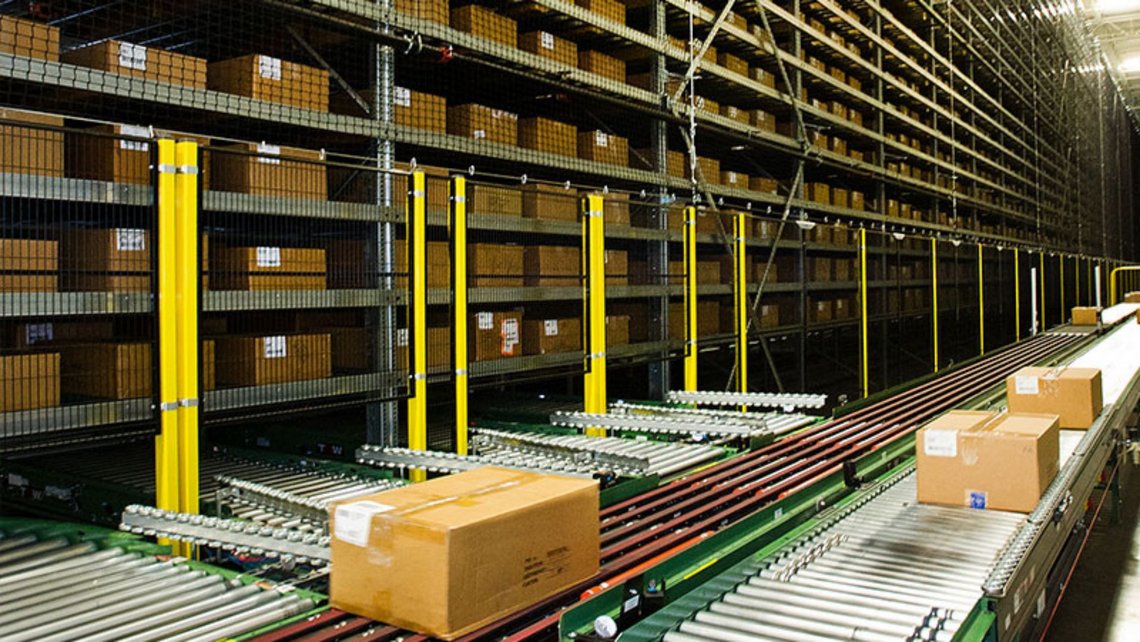
Easy and Accurate Shipping
Shipping cartons are conveyed to the correct dock door and automatically loaded onto trucks, improving the efficiency and accuracy of the shipping process.
Optimize Your Material Handling
TGW Logistics is your partner in achieving new levels of efficiency and performance with automated logistics solutions. Ready to hit your next milestone?
Contact us today
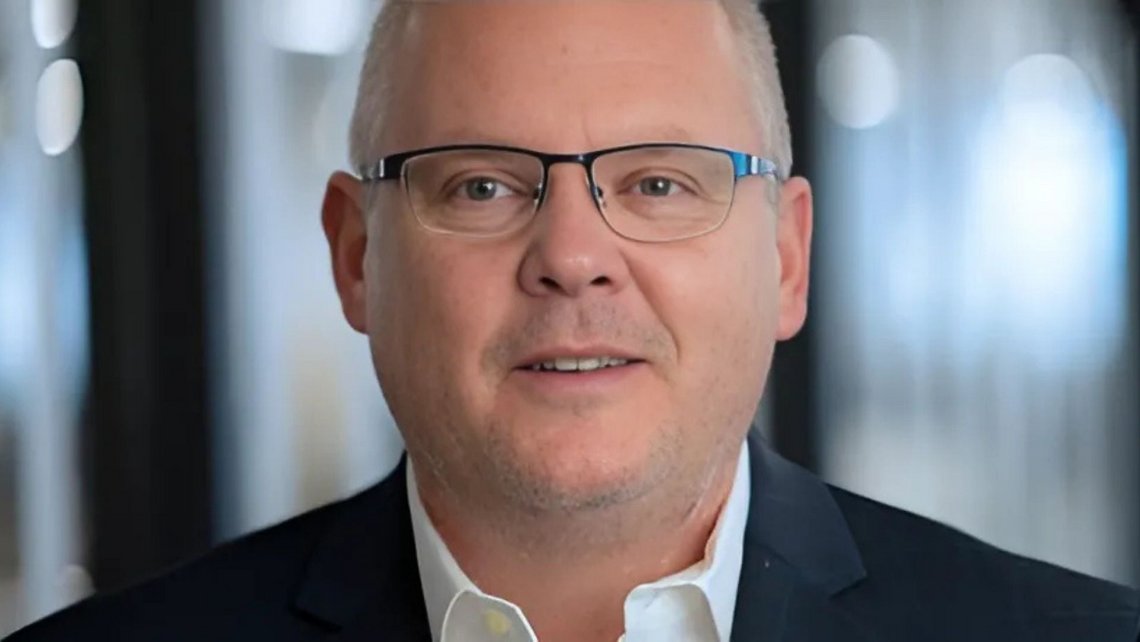
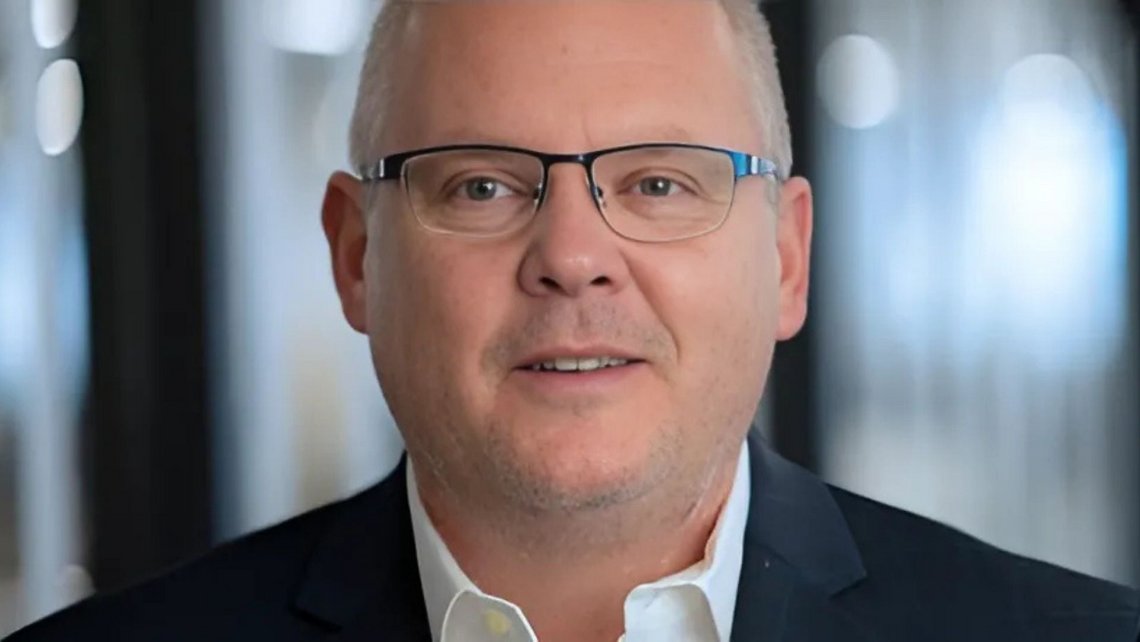
Jeff Rhodes
Director of Sales