![[Translate to North America:] warehouse automation](/fileadmin/_processed_/e/b/csm_TGW_Warehouse_Automation_header_190b49cf82.png)
![[Translate to North America:] warehouse automation](/fileadmin/_processed_/e/b/csm_TGW_Warehouse_Automation_header_190b49cf82.png)
Your Guide to Creating a Seamless Operation
Customers expect fast delivery and high-quality products and will go to the competition if you can’t fulfill their needs, so a high-functioning, scalable logistics system is critical for modern logistics. Warehouse automation provides companies across industry verticals with the systems they need to streamline their operations.
In addition to fulfilling customer expectations, companies must respond to other challenges like labor shortages, shifts in demand, sales growth, and changes in market trends. Overcoming these obstacles requires a scalable infrastructure and the right technology.
However, automation isn’t only about new technology adoption––it’s about solving specific business challenges efficiently. Whether speeding fulfillment for e-commerce businesses, supporting cold storage for grocery distributors, or providing flexible logistics for a fashion company, our automated systems offer tailored solutions that enable a company to reach its goals.
This guide helps businesses discover an automation strategy that fits their needs.
Why Warehouse Automation Could Be Right for Your Business
Modern logistics systems are put to the test in many ways. Labor shortages, demand fluctuation, global supply chain issues, and company expansion are just a few.
America’s aging population presents a particular challenge. Check out these stats from the Population Reference Bureau:
With Americans retiring in record numbers and many approaching middle age, the talent pool for companies with physically strenuous fulfillment operations is shrinking. Plus, our aging population increases demand in industries like healthcare, travel, social service, and hospitality. This boosts opportunities in those industries and allows job-seekers the freedom to be more selective.
- The median age of the country’s population rose from 30 to 39 between 1980 and 2022.
- The 2022 median age was above 40 in 17 states.
- The number of people aged 65 and up is projected to increase to 82 million by 2050.
Unpredictable demand is another pain point. This issue came to a head during COVID-19. Grocery companies struggled to keep up with the spike in online orders. E-commerce retailers also felt the strain of adrenalized demand, especially during the holiday season. Manufacturing companies were unable to stock required parts and supplies.
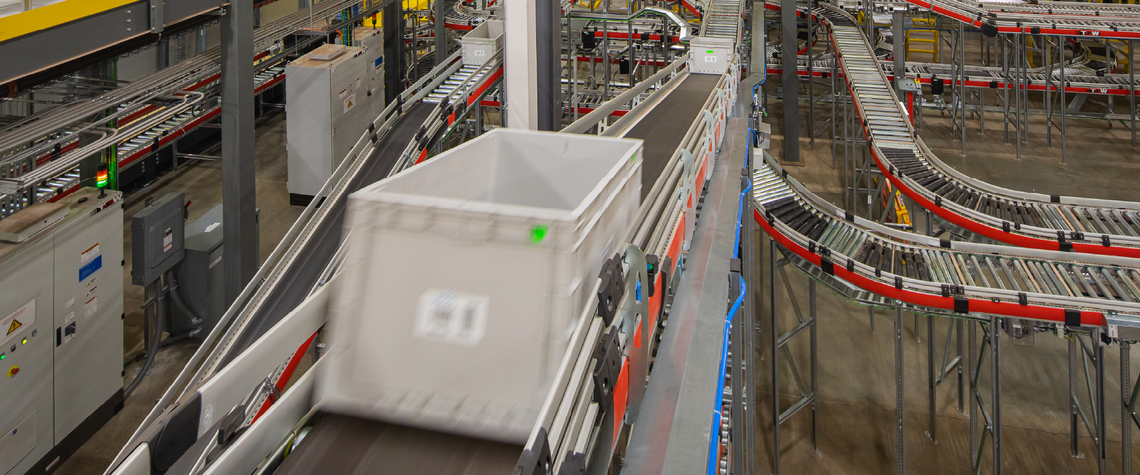
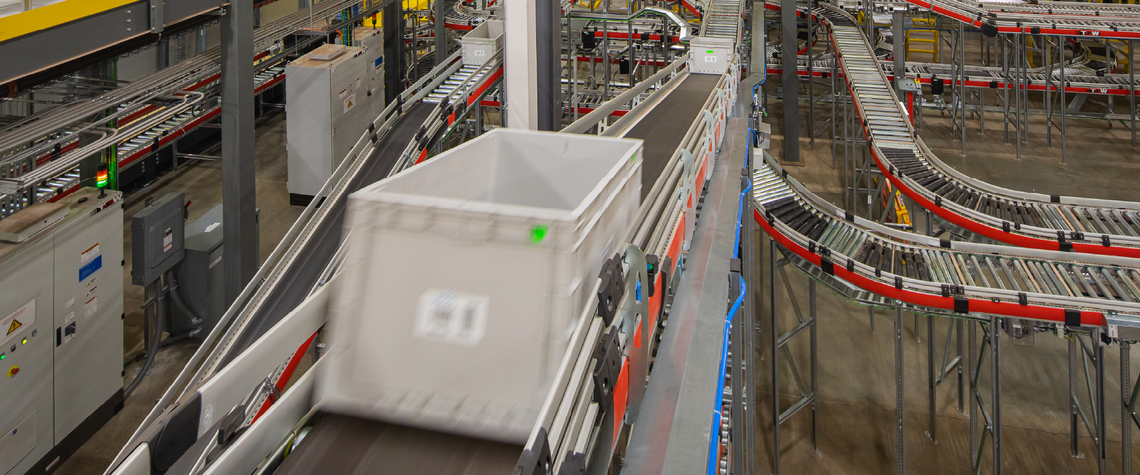
Automation Helps You Meet These Challenges Head On
Warehouse automation offers solutions across your entire material flow, whether you’re facing labor shortages or demand is pushing your fulfillment center to its limits.
Tools like automated goods-to-person picking stations and sorters optimize throughput without needing more workers. Storage systems equipped with autonomous mobile robotics (AMRs) help you meet higher demand with fast product retrieval and restocking.
State-of-the-art automation also provides a high level of flexibility. You can scale your systems as needed and expand order fulfillment operations without pushing your current facility to its limit. And if the warehouse automation operates agnostically to your sales channels, then you build up a resilience to shifts in consumer buying behavior. This future-proofs your distribution center so you reach your long-term goals.
Key Benefits of Warehouse Automation
Successful automation employs a mix of proven technology and customization. Each facility's automated solution looks different, but there are common benefits all companies should focus on.
Efficiency and Cost Reduction
Clunky, outdated systems waste energy and resources, take up space, and put unneeded bodily stress on workers. Logistics automation solves these problems by creating a seamless, less physically demanding material flow, directly impacting operational costs.
Palletizing and depalletizing systems optimize inbound and outbound processes by doing the heavy lifting. This creates a smooth goods-receipt process in your warehouse and ensures you meet shipping schedules going out.
Automated storage and retrieval systems (ASRS) play an essential role in warehouse efficiency. These multi-level structures maximize space utilization, support precise inventory tracking, and increase throughput speeds. In so doing, they improve building footprint efficiency and reduce costs associated with inaccurate or missing inventory counts.
Speed and Accuracy
High customer expectations and strict service level agreements (SLAs) make speed and precision crucial. You can achieve this with automated technology and intuitive human decision-making.
Automated goods-to-person picking systems retrieve items so employees don't have to walk long distances and search up and down aisles for them. These systems often use AMRs and conveyors to transport goods, making employees’ jobs even easier. This allows you to handle more volume by drastically increasing throughput.
In addition to speed, these systems are programmed for accuracy. They ensure the correct items arrive at the appropriate picking stations, track goods with automated scanning, and restock unused items for later use.
Scalability
Modern automation systems allow for a high level of flexibility. Modular components like robotic arms, conveyors, AMRs, and ASRS create a more robust operation as your company grows. Depending on your level of expansion, these tools may allow you to remain in your current facility instead of moving to a larger space or opening a new distribution center.
Warehouse automation also helps you scale during peak seasons when demand skyrockets. You can extend operational hours with a minimized need for additional human labor. It’s also easy to add modular components to increase throughput.
Finally, automated tools seamlessly integrate with your current system. This saves having to make significant upgrades to your infrastructure.
Compliance and Safety
Industries that require stringent compliance and safety measures present additional challenges for warehousing and fulfillment operations. Automation makes these obstacles manageable.
For example, the storing and material handling of food products requires a strict approach. Perishable items must be stored in temperature-controlled environments to be safe for consumption. Warehouse automation monitors this process and tracks expiration dates so expired products are not shipped.
Companies that handle fragile items benefit from gentle handling with technology such as smooth conveyors or AMR transportation. These automated systems eliminate or reduce the need for human lifting or carting, which could damage goods. \
Automated tools are also invaluable in the healthcare industry. They help companies stay compliant and keep consumers safe by managing pharmaceutical inventory. Maintaining accurate records, expiration dates, and regulatory requirements reduces the risk of human error that could lead to injury or illness.
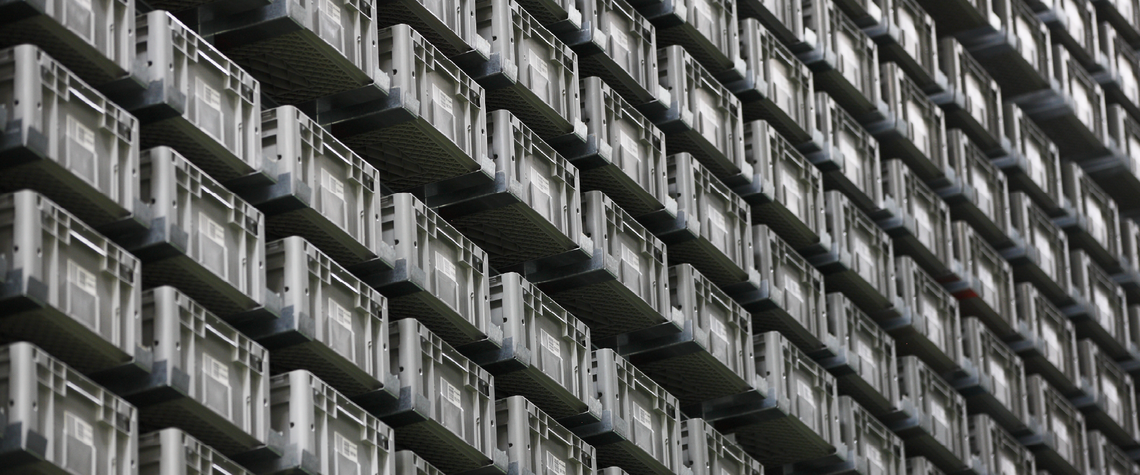
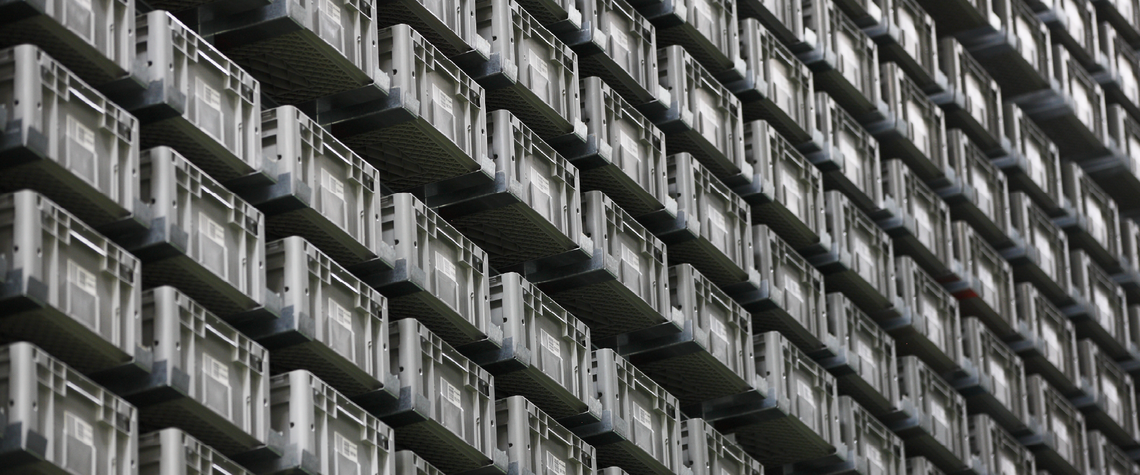
Planning Your Automation Strategy
Automation needs are different for every company. They all have unique challenges and must find solutions that fit their current infrastructure and long-term goals.
If your company is ready to bring automation into the fold, you need a strategy. A good foundation paves the way to a successful warehousing or fulfillment operation designed to meet your needs.
Brownfield vs Greenfield: Which is Right for You?
Your first step in planning an automation strategy is deciding the “where” and whether it will be a brownfield or greenfield site. Here’s a quick breakdown of both:
- Brownfield: This approach involves upgrading an existing facility with automation technology. It includes retrofitting your warehouse with tools that integrate with current systems.
- Greenfield: This approach involves building a new facility with automation in mind. You get to create the infrastructure that fits your exact needs.
Both approaches have pros and cons. You’ll need to consider all angles, including your distribution network strategy, before making a final decision.
Brownfield projects allow you to get new systems up and running quicker and with an overall smaller upfront investment because you do not have to pay for the building. However, your current facility may present space limitations that make it challenging to create the logistics systems you need.
Greenfield projects give you the freedom to more easily plan scalable automation systems for your specific short-term and long-term business needs. However, they require a major initial investment and take longer to complete than a brownfield project because of the addition of building construction timelines and complexity.
Engage Finance Team Early
Adding warehouse automation to your operation is costly, and therefore it’s vital to consider how it fits into your financial strategy. Including your finance department early in the process will shape decisions around your budget and scope of automation and allow you to more easily earn approval on the final warehouse automation proposal.
This includes learning what kind of internal rate of return (IRR) your finance team requires and if they prefer buying or leasing equipment.
This is also your chance to highlight to finance the following long-term cost benefits of automation:
- Higher order picking accuracy reduces human error and increases customer retention.
- A faster fulfillment process increases throughput volume.
- Less reliance on manual labor for difficult tasks decreases labor costs.
- Energy-efficient systems reduce utility and operating costs.
- Reliable systems eliminate costly operational downtime.
- Improved footprint utilization may reduce the need for additional distribution centers.
This information will help the finance team calculate the return on investment (ROI), payback period, and IRR and inform the overall decision-making process.
The finance department also has unique insight into spending, making them a helpful resource in identifying savings opportunities when planning your warehouse automation.
Explore Your Options
Meeting with your finance department allows you to see the path towards approval for automation more clearly. Now, you can start looking into leasing or owning options.
Leasing warehouse automation eliminates the need for a major upfront investment. The money needed to purchase automated systems can be used for other short-term investments that offer a faster and higher ROI.
Purchasing gives you full control of your automated systems, allowing you to expand or reduce them where needed. You also have the freedom to sell your equipment down the road, reducing your total cost of ownership.
There’s no right or wrong answer when deciding between leasing and purchasing. It all depends on your company’s financial strategy and how much cash is available. When making this decision, keep in mind that owning and leasing are better options than not investing at all. Both approaches will help you realize your operational savings.
Steps to Automating Your Warehouse
Bringing your new system to life requires a methodical approach. Planning and initial groundwork will set you up for long-term success.
Here are some crucial steps to consider:
- Assess your workflow: Consider your entire material handling process and pinpoint bottlenecks, repetitive tasks, and error-prone areas.
- Critical data and specs: Gather product dimensions, facility specifications, order history, and growth projections. This data provides a roadmap for both your automation solution design and implementation process.
- Create a flexible design: Choose the automated technologies that meet your needs, based on your data and business strategies, and offer scalability that accommodates future growth.
- Source your suppliers: Your automation supplier must be able to meet your specifications and key performance indicators (KPIs). They should ideally also walk alongside your operations after go-live, providing ongoing support and maintenance.
- ROI analysis: Analyze your solution design to predict when and how it will deliver an ROI.
The steps you take will vary depending on your current infrastructure and future goals. Regardless of your strategy, it’s important to cover all your bases. Consulting with industry experts is a great way to get valuable insights that will inform your process and help you avoid missteps.
Important Considerations During Implementation
Introducing new automation into your workflow is a complex step you must execute flawlessly. A comprehensive approach sets the stage for success.
A Detailed Implementation Plan
Implementing automated systems requires a strategic approach. Working with project managers and defining a step-by-step process is crucial for success. This is especially important if maintaining ongoing operations is necessary.
A highly skilled automation provider makes the process much easier. They’ll know exactly how to manage timelines and risks, work with suppliers, and keep you informed throughout the project.
Labor Need Shifts
Implementing automated solutions may require the addition of highly skilled employees with the training and experience to maintain your new systems. These workers manage warehouse management software (WMS), monitor system performance, and troubleshoot issues.
Warehouse automation also changes the way your current employees work. Eliminating strenuous tasks allows staff to focus on more strategic tasks and promotes a healthier working environment. You’ll need to establish training plans so employees understand how to use and maintain new automation.
Testing and Go-Live
Slowly ramping up your new system ensures that the automation solutions you’ve implemented will work for you. This involves gradually switching from manual to automated workflows. Simulation and emulation software provide valuable insights during the testing phase.
It’s also important to create a plan for after your new automation is live. Decide whether you or an external partner will oversee day-to-day system maintenance. You’ll also need to decide how you’ll manage spare parts or replacements to ensure seamless operation.
Long-Term Benefits of Automation
You may experience some growing pains directly after implementation. However, working with an experienced automation partner makes the stage easier, especially if they'll be directly involved in testing, ramp-up, and training.
The right warehouse automation allows your company to grow with confidence. You can expect these long-term benefits:
- Sustained efficiency gains via faster throughput, accuracy, and higher productivity
- Future scalability with modular systems that allow you to adapt and grow without significant disruptions
- Lower operational costs through energy efficiency, waste reduction, and fewer errors
- Enhanced customer satisfaction and industry reputation
Data-driven insights from your warehouse management software let you know what's working and which areas to improve. Analyzing this data regularly ensures your system is on a fast track to providing long-term benefits.
Discover the Automated Solutions Perfect for You
Though all warehousing and fulfillment operations are different, each must overcome challenging obstacles like labor shortages and unpredictable shifts in market demand. Warehouse automation tailored to your unique needs and goals helps you solve these complex issues.
Reflect on your operational pain points and determine what aspects of your logistics systems fall short. Is your fulfillment process too slow? Are you facing increasing storage issues? Are your operational costs too high? Asking these questions helps you decide which automated solutions best fit your needs.
TGW Logistics uses proven technologies and innovative thinking to create personalized solutions. Our experts work closely with you to find the right balance between automated and manual processes. It’s our goal to make your success possible.
Contact us to set up a consultation with a TGW Logistics expert.