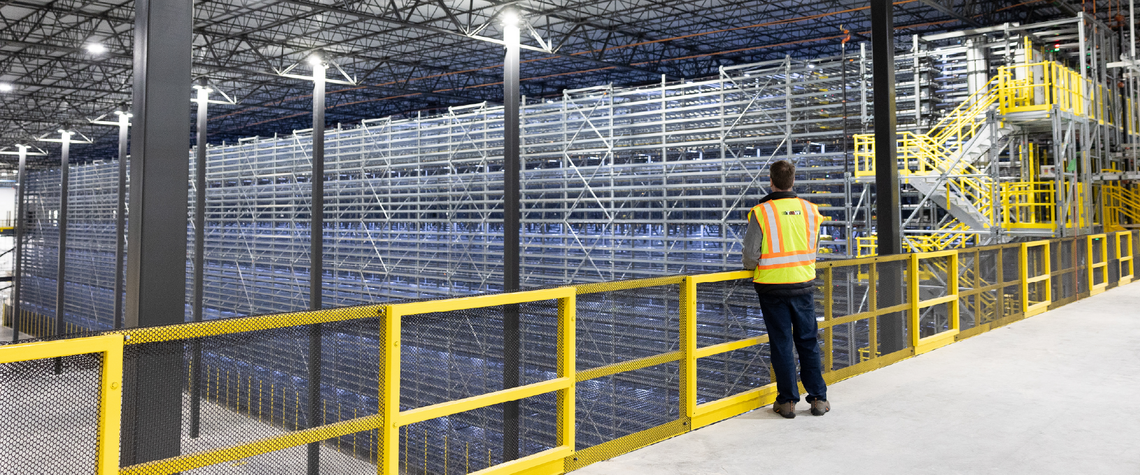
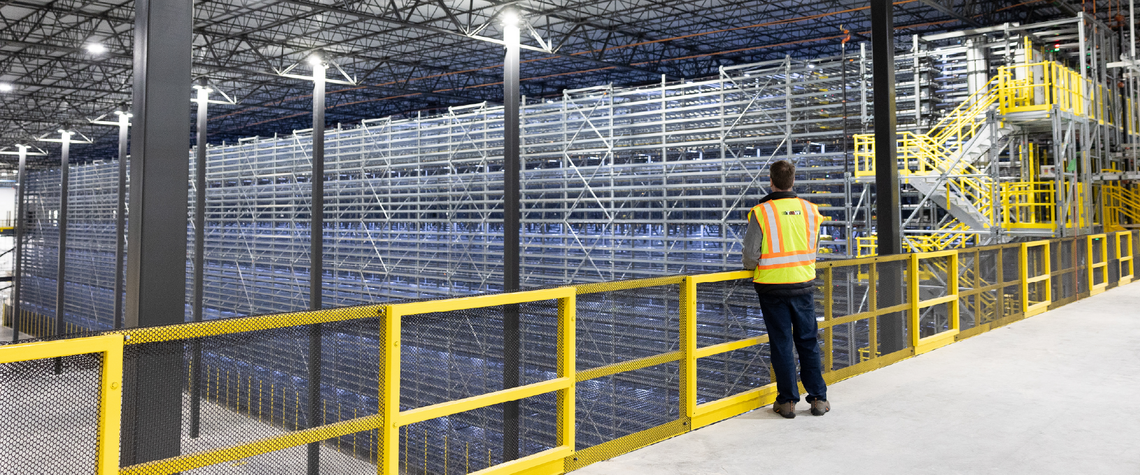
Brownfield vs Greenfield: Finding the Right Warehouse Operations Solutions for Your Company
There’s been a significant shift in consumer demand over the past 20 years. E-commerce changed how people shop for goods and services, ushering in a new era of globalization. The result—a continuous increase in worldwide consumer spending.
To remain competitive, companies must expand to meet the growing demand of their client base, which means rethinking their approach to logistics, opening new distribution centers, and optimizing supply chains by integrating warehouse automation.
When addressing these changes, executives often need help deciding between a brownfield or greenfield expansion. If you’re at this point, it’s essential to understand the intricacies of each approach and have a trusted partner in your corner.
TGW Logistics provides tailored automation solutions for brownfield and greenfield sites. We can help you navigate the process to make the right choice for your company.
Brownfield Projects
When a company expands an existing facility to upgrade its logistics center, it’s called a brownfield project. The process involves retrofitting automated solutions to modernize and enhance storage and warehouse operations without significant disruption.
Brownfield projects require expansion around outdated or underutilized infrastructure. In some cases, brownfield sites are older buildings that require improvements to get back up to code or be able to house automation systems. Before starting the project, the company must assess the property and perform necessary remediation.
Pros
- Expanding an existing facility is often faster and more cost-effective than building a new center.
- A company doesn’t have to search for available land.
- With established labor in place, there’s no need to train new employees.
- Essential warehouse operations can continue during the expansion.
- Redeveloping a facility can adrenalize the local economy.
Cons
- Challenges with the current infrastructure or building condition could make retrofitting complicated.
- The existing layout and infrastructure may limit flexibility and restrict future growth.
- Outdated equipment may have to be sold or written off financially.
- Some business disruption is inevitable due to changes to work shifts or necessary implementation work.
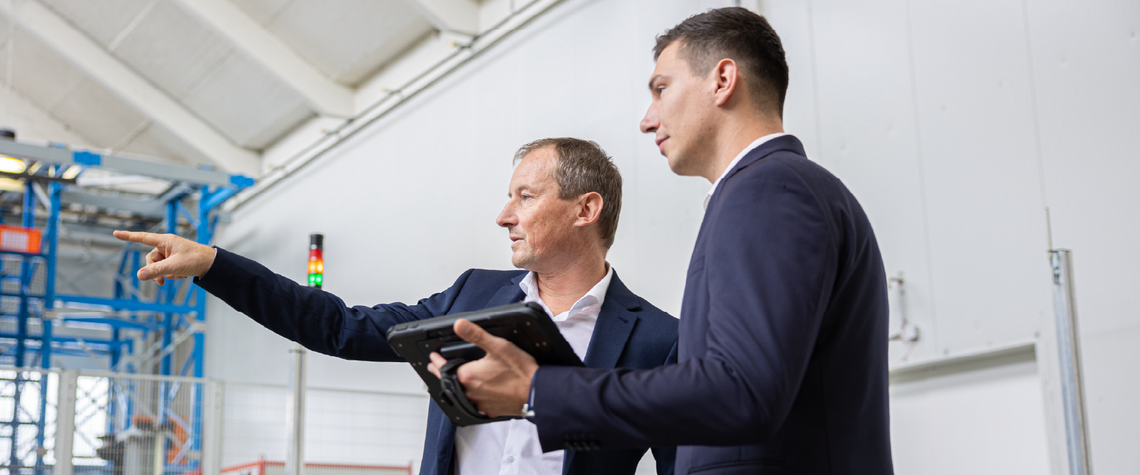
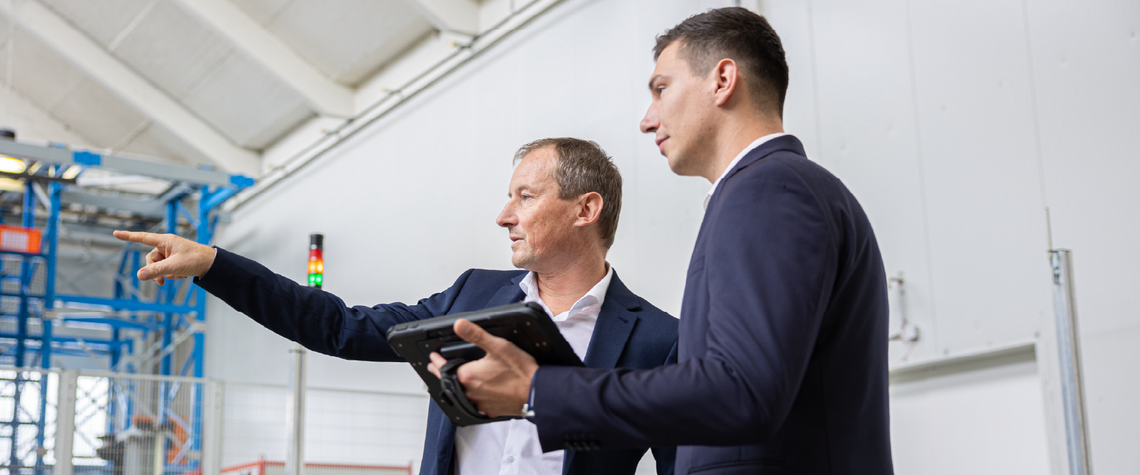
Our Brownfield Solutions
Retrofitting brownfield sites with logistics automation presents unique challenges that require specialized solutions. All new systems must work with the existing environment to ensure optimal efficiency.
TGW Logistics has worked closely with companies to breathe new life into brownfield sites using the following innovations:
- Modular automation can be adapted to fit into available space, bringing accuracy and speed to warehouse operations while creating a scalable environment.
- Retrofitting existing equipment to work with new systems minimizes downtime and offers a cost-effective solution to logistics automation.
- Software upgrade solutions that modernize brownfield sites, allowing legacy equipment to work with new systems.
- Automated mobile robotics increase the speed and accuracy of throughput without requiring significant modifications to the existing floor layout and infrastructure.
Greenfield Projects
A greenfield project involves building an entirely new facility that serves as a company’s logistics center. It involves construction on undeveloped land, allowing for total design flexibility so that a company can meet current and long-term storage and distribution requirements.
Unlike brownfield projects, which retrofit existing infrastructure, greenfield projects offer a blank slate for innovative automated solutions. This allows a company to streamline warehouse operations and maintain control of its operating costs.
Pros
- Greenfield sites offer the freedom to design a fully automated facility that maximizes workflow.
- Complete control of the layout makes planning for future expansion easier.
- Purpose-built systems achieve higher efficiency, accuracy, and speed.
- End-to-end automation supports larger order volume and faster throughput.
- Governments often provide tax incentives for the development of land.
- New facilities bring job opportunities to the area.
Cons
- Land, equipment, and construction costs require a significant initial investment.
- Multiple partners such as building contractors, inspectors, or utility companies each have their own timelines, creating potential delays.
- There’s a risk of underuse if future business growth doesn’t occur.
- Companies may not be familiar with the labor pool in the area.
- Staff must be built from the ground up and quickly trained.
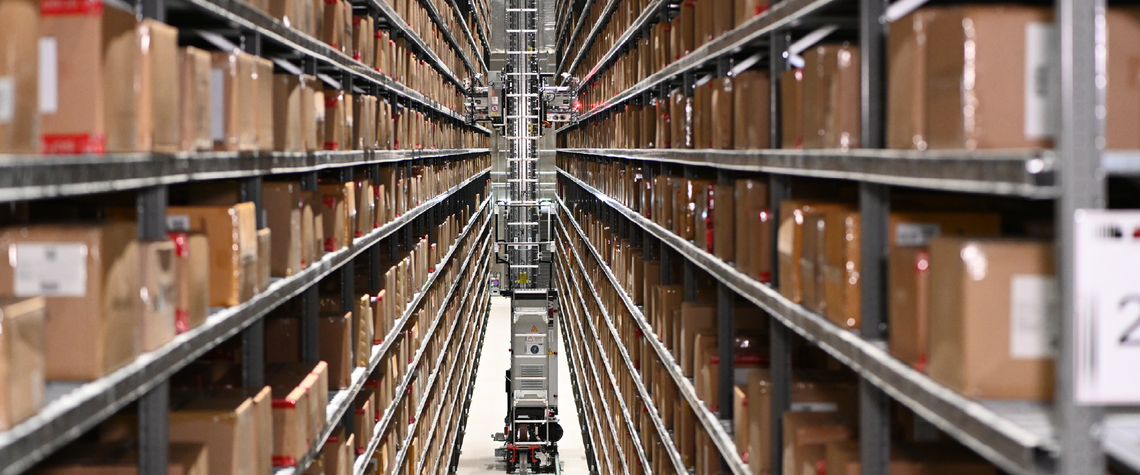
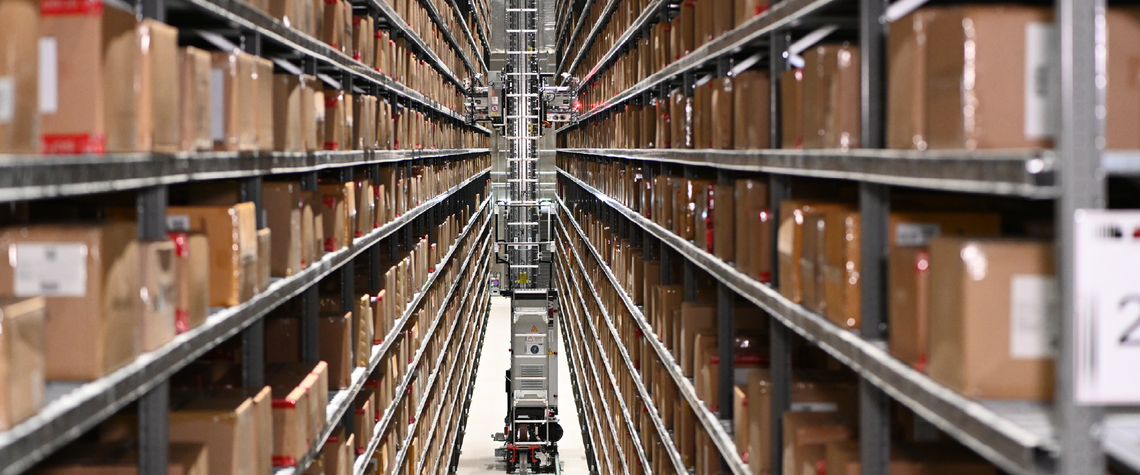
Our Greenfield Solutions
Building a new logistics center offers the opportunity to design and implement customized automated systems. A greenfield project provides flexibility and the opportunity to fully optimize processes for efficiency, scalability, and innovation.
Through partnerships with companies undergoing massive expansion, TGW Logistics has first-hand experience with the following greenfield innovations:
- End-to-end automation optimizes all warehouse operations, from goods receipt to shipping.
- Scalable systems future-proof a new logistics center by creating a flexible environment that can facilitate increasing demand.
- A data-driven infrastructure allows for real-time monitoring, ensuring efficiency and pinpointing areas that can be improved or scaled.
- Seamless integration of automation technology and software allows all systems to work together immediately.
- Customization provides the design layout and automation required to meet the needs of a specific industry.
Choosing Between Brownfield and Greenfield
The right approach to your new logistics center depends on many factors. These include your current infrastructure, the size of your warehouse operations, and the company’s long-term goals.
Here are some key considerations you’ll need to address.
A wise first step is determining whether it’s more cost-effective to retrofit an existing facility or build a new one. TGW Logistics' clients typically do a complete 10-year cash-flow analysis and look at the return on investment (ROI), internal rate of return (IRR), and other metrics to get a financial overview.
Planning for growth is critical when deciding between a greenfield and a brownfield site. You’ll need to consider whether your current infrastructure can meet demand forecasts or if future-proofing requires a new facility.
Determining how much downtime your company can afford is essential before making a final decision. Getting a brownfield site up and running is typically quicker than building a new greenfield facility. Companies often maintain at least partial operations while retrofitting an existing logistics center.
Conduct a thorough analysis of your current logistics center and determine if the facility has enough space for retrofitting automated solutions. Examine your long-term goals and industry trends to decide whether you should stay where you are and upgrade or develop a new facility to meet your needs.
Greenfield and brownfield projects carry different levels of risk. Evaluating every project stage and creating a cost-risk analysis will help your company make an informed decision.
TGW Logistics' Approach: It’s Possible
Choosing between a brownfield and greenfield project to facilitate expansion isn’t easy. Weighing the options may leave you feeling somewhere in the middle.
The good news is that brownfield and greenfield projects aren’t mutually exclusive. Success is possible using a hybrid approach–upgrading existing facilities while planning for new sites.
Our End-to-End Portfolio
TGW Logistics offers innovative solutions that fit any operational strategy. We use the same proven technologies for brownfield and greenfield projects, tailoring them to your business needs.
Our experts have the knowledge and experience to integrate technology into existing systems or design new facilities that leverage cutting-edge automation.
Brownfield Case Study
TGW Logistics partnered with Jasco, a specialist in US consumer electronics and lighting, to expand their fulfillment center. We integrated new split case picking automation and Stingray shuttles to streamline their good-to-person process and cut operating costs. Our ergonomic workstations reduce physical stress for their employees and reduce the amount of walking needed to complete tasks.
Greenfield Case Study
When Puma invested in a new central distribution center, they turned to TGW Logistics for help. Their goal was to combine B2C and B2B distribution centers into one hub. Our automated solutions helped streamline their retail and wholesale fulfillment operations and support consistent output at peak times.
Optimize Your Warehouse Operations With TGW Logistics
Whether you’re planning a brownfield or greenfield project, TGW Logistics can provide expert guidance. We’ll help you navigate the process and implement scalable solutions for each step of the automation journey.
Contact us to learn more.