Richard Wolf & TGW Logistics
Bringing Richard Wolf’s New Distribution Center to Life With Warehouse Automation
Richard Wolf’s Consolidated Healthcare Logistics Project
Richard Wolf GmbH is a full-service provider of sustainable and innovative medical devices and instruments used in endoscopic procedures. From its humble beginnings in 1906 as a family enterprise, the company has grown into an international operation with 18 branches employing over 1,700 workers worldwide.
After consistent growth, Richard Wolf decided to consolidate several small warehouses into an automated logistics center in Knittlingen, Germany. The aim was to create a state-of-the-art storage and distribution facility that relies on warehouse automation to streamline material flow and promote a more efficient order picking process. To achieve this, they needed a partner who could integrate automated solutions for the handling and storing of its highly sensitive products.
Project Targets
- Streamline Richard Wolf’s healthcare logistics operation using warehouse automation
- Increase employee productivity and reduce errors by implementing state-of-the-art technology and ergonomic workstations
- Support more efficient and timely goods receipt, order picking, order consolidation, and shipping processes
- Create a flexible and scalable system that facilitates future growth
How TGW Logistics’ Solutions Made it Possible
TGW Logistics faced the unique challenge of developing Richard Wolf’s entire installation without electrostatic loading. In addition, consolidating its warehousing and distribution operation into a single facility had to offer a significant performance upgrade.
Automated Healthcare Logistics for Sensitive Medical Materials
Richard Wolf’s electronic medical devices contain high-resolution cameras designed with strict quality standards. To protect these sensitive products, we had to ensure the absence of electrostatic charges during the material flow process.
To accomplish this, we implemented anti-static brushes on conveyor in-feed and out-feed transfers. An integrated lighting mechanism lifts the steel brushes so totes can swipe them, creating a discharge. Storage shuttles with vulcanized wheels also contain these brushes.
A State-of-the-Art Storage Solution
Richard Wolf required a storage capacity of 45,000 items in the new distribution center. They also wanted a system that eliminated the need for employees to walk long distances. To solve this, TGW Logistics implemented a Stingray shuttle system with three aisles and KingDrive conveyor technology.
When goods arrive in the receiving area, they’re repacked into totes, and a warehouse management system reports the goods to the material flow control system. Then, conveyors transport goods into the Stingray shuttle aisles. In the three-aisle warehouse, 48 shuttles operate on 16 levels. Incorporating stacking and de-stacking devices allowed for maximum storage capacity.
Efficient Goods-to-Person Picking
In addition to storage solutions, the new shuttle system helped create a seamless goods-to-person picking operation. Before consolidating its warehouses, Richard Wolf’s employees spent too much time walking and manually picking products. With the new shuttle system implemented, goods are retrieved and transported to eight ergonomic picking workstations at a rate of 1,600 totes per hour. Once picked, products proceed to the packaging area, where they’re placed onto pallets and roll containers for direct shipment to the customer.
Putting Energy Efficiency Front and Center
TGW Logistics incorporates energy recovery and efficiency aspects into our technologies, cutting client costs and maximizing warehouse automation systems' operational longevity. This efficiency is achieved through the automatic shutdown of system areas that aren’t required, energy recovery, and an energy-saving mode.
With innovative automated solutions in place, Richard Wolf maintains operational efficiency at its Knittlingen center and has the infrastructure in place to handle future growth.
“Since the implementation of the automated small parts warehouse, the system has been running without any major breakdowns. The TGW Logistics service hotline is always available and has been able to resolve all incidents competently, quickly and sustainably. We are very happy to be prepared for the challenges of the future with the modern system”, says Raphael Kiefer, Specialist for Lean Management at Richard Wolf.
Take Your Logistics System to the Next Level
At TGW Logistics, our goal is to make growth possible. Our forward-thinking approach to automated solutions will transform your operation and put your company on a fast track to success.
Contact us today
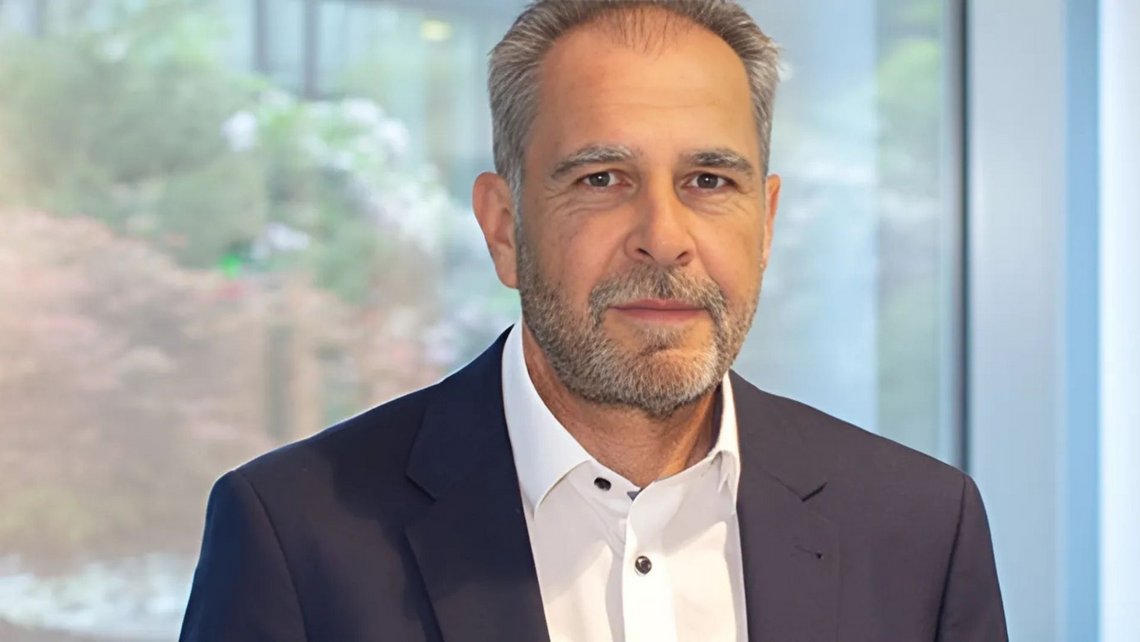
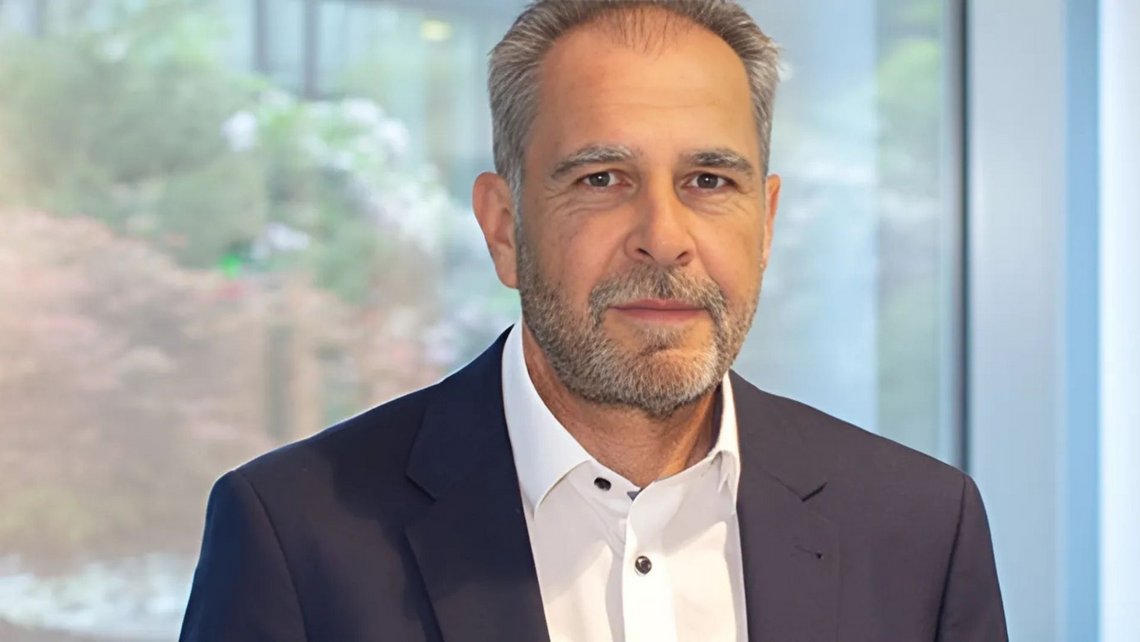
Erich Schlenkrich
Vice President Business Development Industrial & Consumer Goods
Como fundación empresarial con sede en Austria, TGW Logistics es líder mundial en automatización y logística de almacenes. Como leal integrador de sistemas, con más de 50 años de experiencia, ofrecemos servicios integrales de diseño, implementación y mantenimiento de centros logísticos, impulsados por mecatrónica, robótica y soluciones avanzadas de software. Con más de 4.500 empleados en Europa, Asia y América del Norte, combinamos experiencia, innovación y dedicación centrada en el cliente para ayudar a que su negocio siga creciendo. Con TGW Logistics, it's possible transformar tu logística de almacenamiento en una ventaja competitiva.