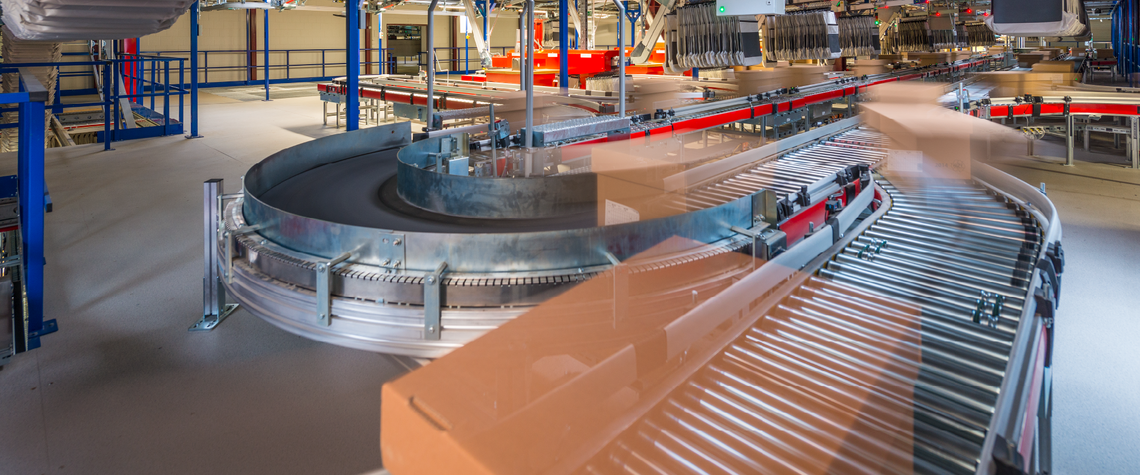
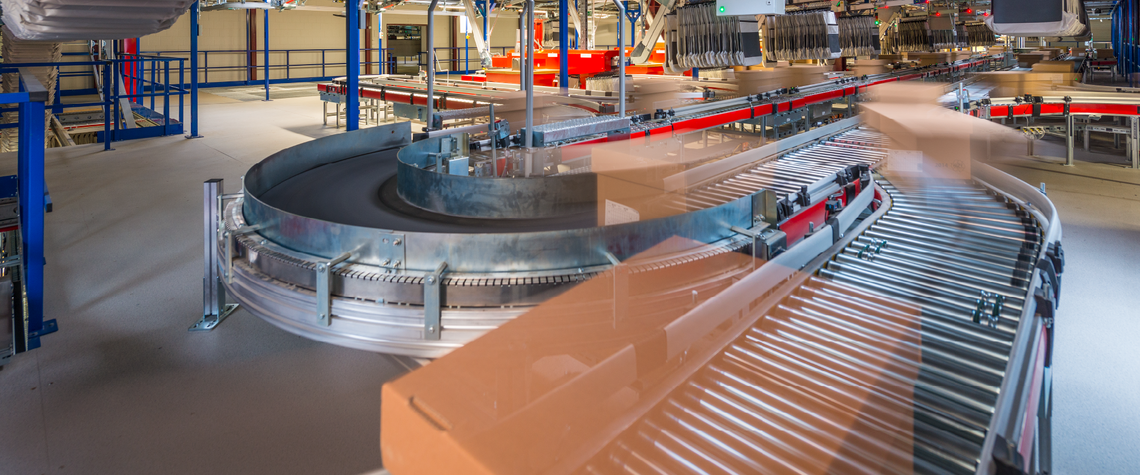
and Its Role in Warehouse Logistics
The shift to online shopping forever changed how companies fulfill their customers' needs. Speed, efficiency, and accuracy are mandatory, and companies are reacting to ever-increasing consumer demand by implementing goods-to-person automation to meet their needs. The result is an automated material handling equipment market that’s forecasted to grow by 8.9% between 2024 and 2029–that’s an increase of over $18 billion in four years.
Automation can optimize the material flow of goods from the moment they arrive at a warehouse to when they ship to customers, an invaluable resource in a consumer market where every second counts.
TGW Logistics understands the need for efficient, seamless throughput. We designed our automated systems to immediately integrate arriving goods into a warehouse’s workflow. This level of efficiency sets the tone for a seamless process throughout the warehouse. But what happens after that?
Let’s walk through a typical material flow in a fulfillment center to better understand how goods-to-person automation can transform logistics.
Inbound Logistics: Where it All Starts
The first stage in the material flow journey begins when goods arrive at a warehouse. Depending on the company, “goods” may include products ready for sale or materials required for production.
Goods typically arrive by truck and are unloaded at a docking bay, where automation already enters the material flow. By unloading materials quickly and efficiently, automation creates a seamless intake process and prevents congestion at the loading dock. It also supports a smooth transition from the truck to the logistics center.
Once in the warehouse, goods get processed and sorted. Tools such as Radio Frequency Identification (RFID), barcodes, and QR codes make logging items into inventory fast and error-free. This level of accuracy is critical for tracking goods as they move to storage areas or on to their next destination in the material handling process.
Automated technologies support a quick and accurate inbound process. Goods receipt systems make unloading easier on workers and reduce the risk of injury.
Inside the warehouse, sorting systems identify and sort products based on key factors like type, quantity, and final destination. This degree of precision ensures products are stored exactly where they need to be or are prepared for the next phase of their journey through the warehouse.
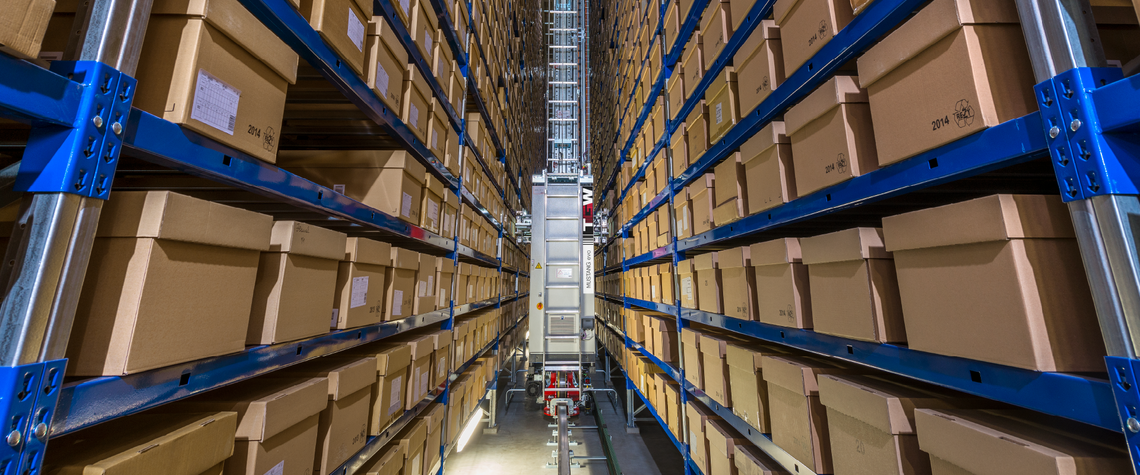
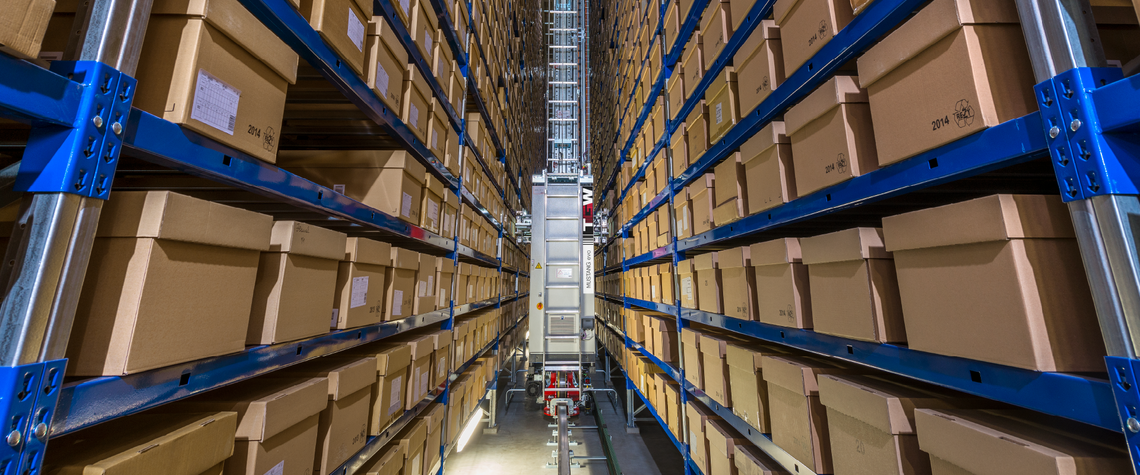
Flexible Storage Systems
State-of-the-art automated storage is crucial to a distribution center’s success. It supports successful inventory management, optimizes warehouse space, and streamlines retrieval and fulfillment. In a world of fierce consumer demand, companies must look to automation for seamless storage solutions or risk losing business to their competitors.
Automated Storage and Retrieval Systems (ASRS)
When goods are processed and logged into a warehouse management system, they’re moved into storage via ASRS. These systems include different automated components that work together to transport goods to high-density storage units and retrieve them during fulfillment.
Here’s a breakdown of the components commonly found in automated storage and retrieval systems:
- Storage racks: These multi-level systems include racks and aisles that house items until needed.
- Automated shuttles: These robots move vertically and horizontally through the racking system to retrieve or deposit items in designated storage spaces.
- Conveyors and/or AMRs: After items are retrieved from the storage rack by shuttles, they’re placed on automated conveyors or autonomous mobile robots (AMRs) that transport them to picking workstations or shipping areas.
- Warehouse management systems (WMS): This software controls an entire warehouse operation, including the ASRS.
Dynamic Storage Allocation
The real power of ASRS lies in its ability to allocate storage dynamically based on real-time data. Dynamic storage allocation supports storing goods in the most efficient spots based on demand, inventory levels, and size.
This approach provides a more efficient storage and retrieval system than storing goods in fixed locations. Storing high-demand items closer to picking areas speeds the retrieval process, while less frequently needed goods are placed in deeper storage.
This data-driven approach improves operational efficiency by reducing the travel time needed to retrieve an item and maximizing available space. It allows a warehouse to handle more inventory without expanding its footprint.
Fast and Reliable Order Processing
In addition to high demand, customer expectations put a lot of pressure on a company's logistics systems. Fast, accurate order delivery is the standard, and customers will quickly seek out other brands if their needs aren’t met.
Once goods move to a warehouse’s storage system, they await order processing. Automated goods-to-person picking is crucial at this stage. It ensures items move quickly and accurately through the material handling flow.
A Successful Goods-to-Person System
The warehouse management system (WMS) triggers an automated picking process when a new order is received. Items are then retrieved by shuttles and transported via conveyor or AMR to picking workstations. The WMS ensures the correct items reach their allocated stations.
Automated conveyors also play a crucial role in efficient order processing. They transport goods from storage to picking workstations and return empty totes or cartons to the storage system. They also play a factor in the sequencing of orders, ensuring that pickstations do not become starved or backed up. This synchronized process maximizes throughput and maintains organization without human intervention.
At workstations, employees manually pick items from the totes or cartons. Computers show them the item type and quantity that needs to be processed for fulfillment. For example, PickCenter One workstations facilitate 1:1 picking, which means there’s only one source and one target. This makes for extremely accurate order fulfillment.
Companies enjoy several benefits of automating the material handling of goods at the order processing stage. A significant reduction in picking times, higher accuracy, and faster order fulfillment all boost customer satisfaction and improve retention.
Packing and Value-Added Services (VAS)
The next step in the material handling journey involves preparing goods for shipping. Items move from picking to packing stations. Here, automation supports efficient packaging so each product arrives at its destination and remains safe during transport.
Automated packaging systems meet the unique needs of each logistics center. Some systems are semi-automated, making packing more manageable for employees. Others are fully automated and require little to no human interaction. In addition, automated packaging systems are designed to accommodate specific product types and sizes.
Offering value-added services such as inserts, coupons, and custom holiday wrapping can be difficult. Automated systems powered by warehouse management software seamlessly work these processes into the material flow without causing backups.
Let’s look at the steps involved in fully automated packaging:
- Goods are scanned at packing stations to ensure accuracy.
- The automated system prepares boxes suitable for the packed item size.
- Either robotic arms place items in the box or a box is built around the items.
- Protective material is added to the box to secure the item during shipping.
- Boxes are automatically sealed with packing tape, adhesives, or straps.
- Packed boxes are weighed and labeled for tracking.
- Automated cameras provide quality control by inspecting boxes to ensure correct packing.
- Conveyors transport boxes to shipping areas.
This intricate system provides many benefits to warehouses with high throughput. Automation speeds the packaging process and significantly reduces human error. It also decreases material waste by packaging items in appropriately sized boxes, which promotes supply chain sustainability and lowers shipping costs.
Accurate Outbound Logistics
The next step in the material handling process involves shipping goods to their destination. However, many things must happen before packaged items leave the warehouse. Automation supports a well-organized, error-free outbound process so packages are prepared and shipped on time.
Here’s a rundown of an automated outbound logistics system:
- Packages are automatically grouped and sorted by destination to consolidate orders by logical delivery routes.
- Sorters place each item in the correct shipping lane.
- Packages are measured via camera to ensure they meet carrier regulations.
- The automated system provides the best packing configuration for loading items onto trucks.
- Automated palletizing robots stack boxes safely so they remain sturdy during shipping.
- Conveyors make loading pallets into trucks fast and easy.
Warehouse management systems also play an essential role in outbound logistics. They generate shipping labels, provide tracking updates, and coordinate loading times based on carrier schedules. Warehouse analytics software also pinpoints areas of improvement so companies can work toward a more efficient system.
Returns Processing
Product returns are inevitable. Companies must have systems to facilitate the smooth transfer of items back into their fulfillment center. Automated systems simplify this with material handling solutions that support an organized and efficient workflow.
Customers return items for different reasons. A pair of jeans may not fit correctly, or a product may sustain damage at some point during the fulfillment process. These factors come into play when a company processes a return and provides a refund or exchange.
Here’s a walkthrough of a return process supported by automation:
- Returned items are scanned into the warehouse management system to confirm that the item matches the original order.
- Automated conveyors sort items based on the reason for the return.
- Sensors weigh and inspect items to determine their condition.
- Conveyors or AMRs automatically route undamaged items to storage or workstations for manual inspection and redistribution.
- Damaged items are routed to repair or disposal areas.
- Refunds are triggered based on the condition of an item.
- New orders are auto-generated if the customer requests an exchange.
This seamless process supports fast returns, keeps a warehouse’s inventory up-to-date, and maximizes storage space. Automation also offers sustainable solutions by sorting damaged goods and moving them to shipping areas for transport to recycling or donation centers.
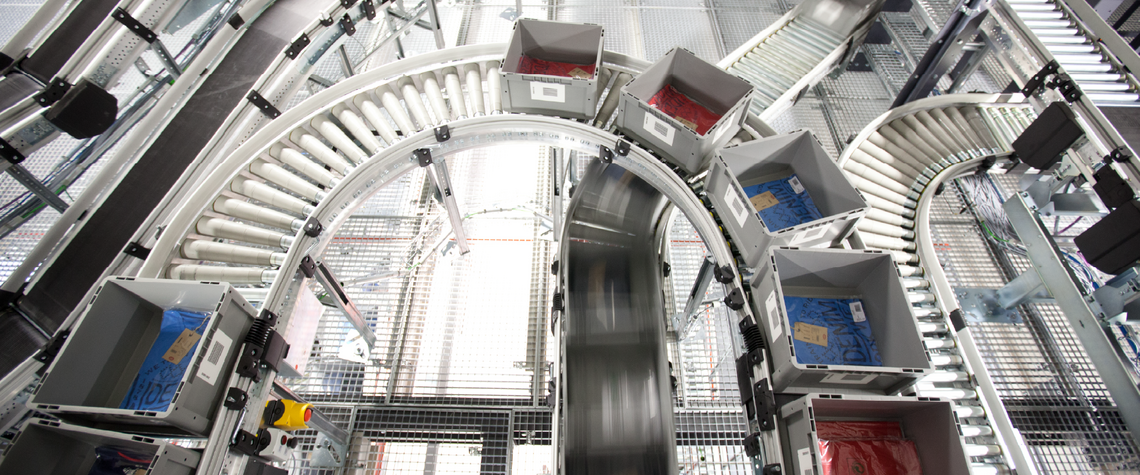
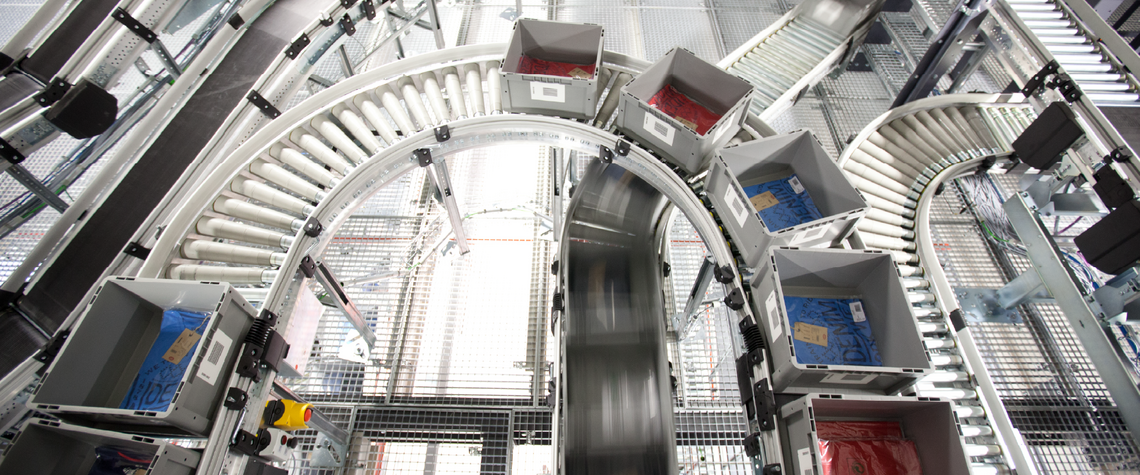
Supporting Systems
Automated logistics systems provide the infrastructure needed to streamline the entire material flow in fulfillment centers. Each system is tailored to meet industry demands and solve a company’s unique needs, so every automated system looks different.
However, several critical components help maintain efficiency throughout most automated warehouses.
All the moving parts of an automated warehouse must come together and operate as a single, unified system. A warehouse management system makes it possible. This crucial software is a fulfillment supply chain's brain and control center. A successful operation isn’t possible without it.
A WMS helps warehouse managers oversee every step in the logistics process and ensures the optimal efficiency of every system.
The primary functions of a WMS include:
- Managing inventory throughout the material flow
- Monitoring automated goods-to-person systems
- Assisting employees at picking workstations
- Tracking goods throughout the warehouse
- Measuring the productivity of automated systems and human workers
- Optimizing space in storage systems
- Streamlining inbound and outbound logistics
In addition to these functions, a WMS offers real-time data analysis, which allows a company to fine-tune its process, cut costs, and scale its operations to meet growing demand.
Advancements in automated technology have transformed the way we think about logistics. High-performance robotics provide a level of speed and efficiency that fulfillment centers couldn’t achieve in the past.
Autonomous Mobile Robots (AMRs) and Automated Guided Vehicles (AGVs) are becoming more commonplace in warehouses today. They assist workers with order picking and transporting items across large facilities. This reduces worker stress, reduces costs, and improves accuracy.
Robots are particularly useful in Automated Storage and Retrieval Systems. They eliminate the need for manual order retrieval and are highly adaptable to demand fluctuations, making them indispensable in high-volume fulfillment centers that require consistent throughput.
For decades, warehouses have used conveyors for production and fulfillment purposes. However, the old systems were clunky and one-dimensional. Today’s automated conveyors add a new element of efficiency, speed, and scalability.
Conveyor systems touch almost every point in the material handling process. They facilitate seamless unloading during inbound operations, transport goods to the correct location, and assist with picking, packing, and moving items in and out of storage.
A big advantage of conveyors is that they work seamlessly with other automated systems like robots and workstations. Plus, different types of automated conveyors are designed to handle a wide variety of items. This allows companies to integrate the right conveyor system for their operation.
Automate Material Handling in Your Warehouse With TGW Logistics as Your Partner
TGW Logistics provides material handling automation to optimize every link in your supply chain. Our experts will work closely with you to seamlessly integrate automated systems across your logistics network. We have the knowledge and experience to streamline your processes and improve operational efficiency.
Schedule a consultation with us and discover how we’ll enhance your warehouse’s performance and drive future growth. Contact TGW Logistics today.